Project Subtitle:
Project Description:
The clients came to visit the Transformations Coppersmith Way Development in Townsend on the National Solar Tour in October several years ago. They were interested in building an energy efficient historic looking home. They had built their existing home some 20 years previously and wanted to upgrade to today's standards.
With the husbands engineering background, he was very interested in the details that were evolving on how to super-insulate a home and then power it with renewable energy. Several times he visited the Coppersmith Way project to see what was the latest and greatest.
Kraus Fitch architects worked with the Clients to create a beautiful layout that included a first floor master, two additional bedrooms, an open floor plan with vaulted ceilings and a sun room towards the rear. The owners incorporated a "barrel roll" in clapboards on the front of the home. We used Hardy Plank siding on the other three sides. The first floor windows had 12 over 12 panes of glass. The front door had bulls eye glass over it. A large chimney facade stands proudly in the center of the main roofline.
With the front of the saltbox facing north, we were able to get 14.4 kW of SunPower panels on the rear roof facing south. This helped our Energy Star rating to come in at a -9. The home is an all electric home. During 12 months of living the utility bills show only 5,331 kW hours of electricity were consumed. During the same time the solar electric system generated 15,867 kW hours of electricity, or 10,536 more kW hours than it consumed. At a conversion rate of .33 kW per mile, this allows for 31,900 miles of electric driving. With a zero energy home, we can reduce our share of 48% of the carbon associated with the building sector. With energy positive homes like this we can also reduce our share of the 33% of carbon associated with the transportation sector!
The home has a heat recovery ventilation system and three mini-splits (two on the first floor and one on the second floor) which supply quiet heating and cooling to the home. An air source heat pump water heater in the basement supplies ample hot water for the home.
The walls are 12" double studded 2x4's with a 5" gap between the two walls. A 1.5 inch layer of foil faced rigid was added to the outside. On the inside layer of the sheathing we sprayed a 3" layer of closed cell foam. The remaining wall was filled with low density foam. The cavity insulation value of this assembly was R-60. The R-20 basement walls have 3.5" of closed cell foam and a fire protection coat of paint. The slab has 2" of rigid for a R-Value of 10. The R-5 windows are triple glazed and filled with krypton gas.
The home received an Energy Star Tier 3 certification in Massachusetts and construction was completed in the fall of 2011.
Building Type Summary:
Address:
Elevation:
Lat. / Long.:
Location Type:
Köppen Climate Type:
Climate Region:
Solar Insolation:
Annual HDD :
Annual CDD:
HDD Base Temp:
CDD Base Temp:
Occupancy Type and Details:
The home was occupied for the 12 month period. There are 2 members in the household.
Conditioned Floor Area:
Multiple buildings?:
Total number of units in project (all buildings):
Total floor area of project (all buildings):
Historic?:
Completion date:
Energy Star Score:
Annual renewable energy generated:
Electric Utility Company:
Electricity amount (imported from grid):
Electricity amount (credited or exported to grid):
Net electricity usage (purchased electricity):
Subslab assembly:
2" rigid, R-10
Slab edge assembly:
2" rigid, R-10
Foundation wall assembly:
3.5" closed cell foam, R-20
Above grade wall assembly:
12" double stud walls with 9" open cell foam (R-33) and 3" closed cell foam (R-18); 1.5" foil faced poly-iso on the exterior of the sheathing with strapping (R-9). The total cavity insulation of the walls is R-60.
Flat attic assembly:
18" cellulose, R-67
Cathedral ceiling assembly:
2" closed cell foam, R-12, followed by 14 inches of R53 blown in cellulose. Total cavity of R-65.
Space heating - Manufacturer & Model:
Space cooling - Manufacturer & Model:
Domestic hot water - Manufacturer & Model:
Ventilation - Manufacturer & Model:
Process:
Kraus Fitch architects worked with the Clients to create a beautiful layout that included a first floor master, two additional bedrooms, an open floor plan with vaulted ceilings and a sun room towards the rear. The owners incorporated a "barrel roll" in clapboards on the front of the home. We used Hardy Plank siding on the other three sides. The first floor windows had 12 over 12 panes of glass. The front door had bulls eye glass over it. A large chimney facade stands proudly in the center of the main roofline.
Finances Description:
Cost of building construction, excluding design fees, site preparation, and unconditioned space was $360,465. The square footage of the conditioned space, measured from the exterior is 3,927 square feet. This includes the conditioned basement but not the garage. The cost per square foot, including the PV system was $91.79.
Total Cost of Project:
NESEA Awards:
NESEA Zero Net Energy Building Award 2013 runner-up
Energy Use and Production Documentation:
Subslab R-value:
Slab edge R-value:
Foundation wall R-value:
Above grade wall R-value:
Flat attic R-value:
Cathedral ceiling R-value:
Average window U-factor:
Solar Heat Gain Coefficient:
Cost per square foot of Conditioned Space:
Project Photos:
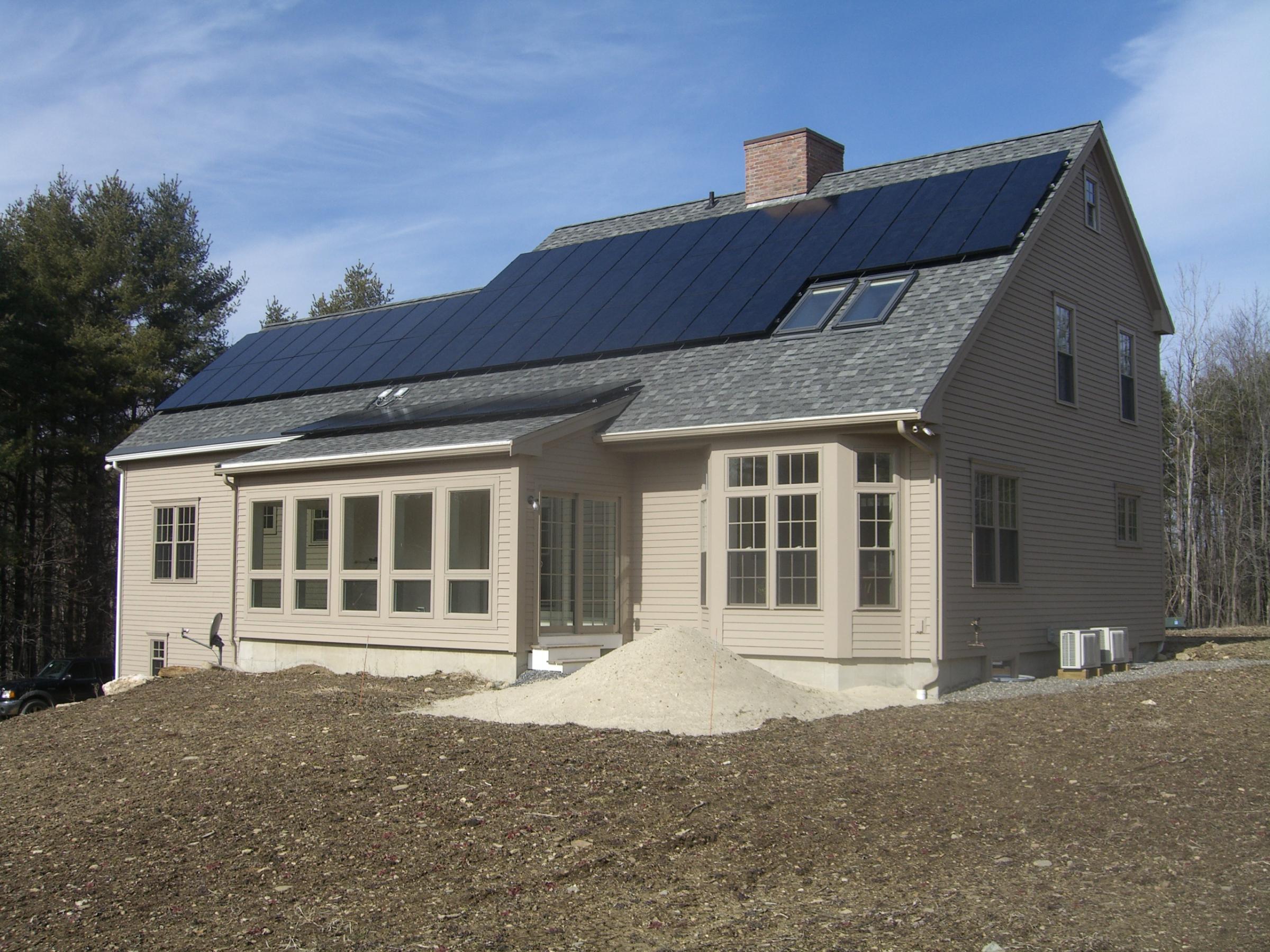


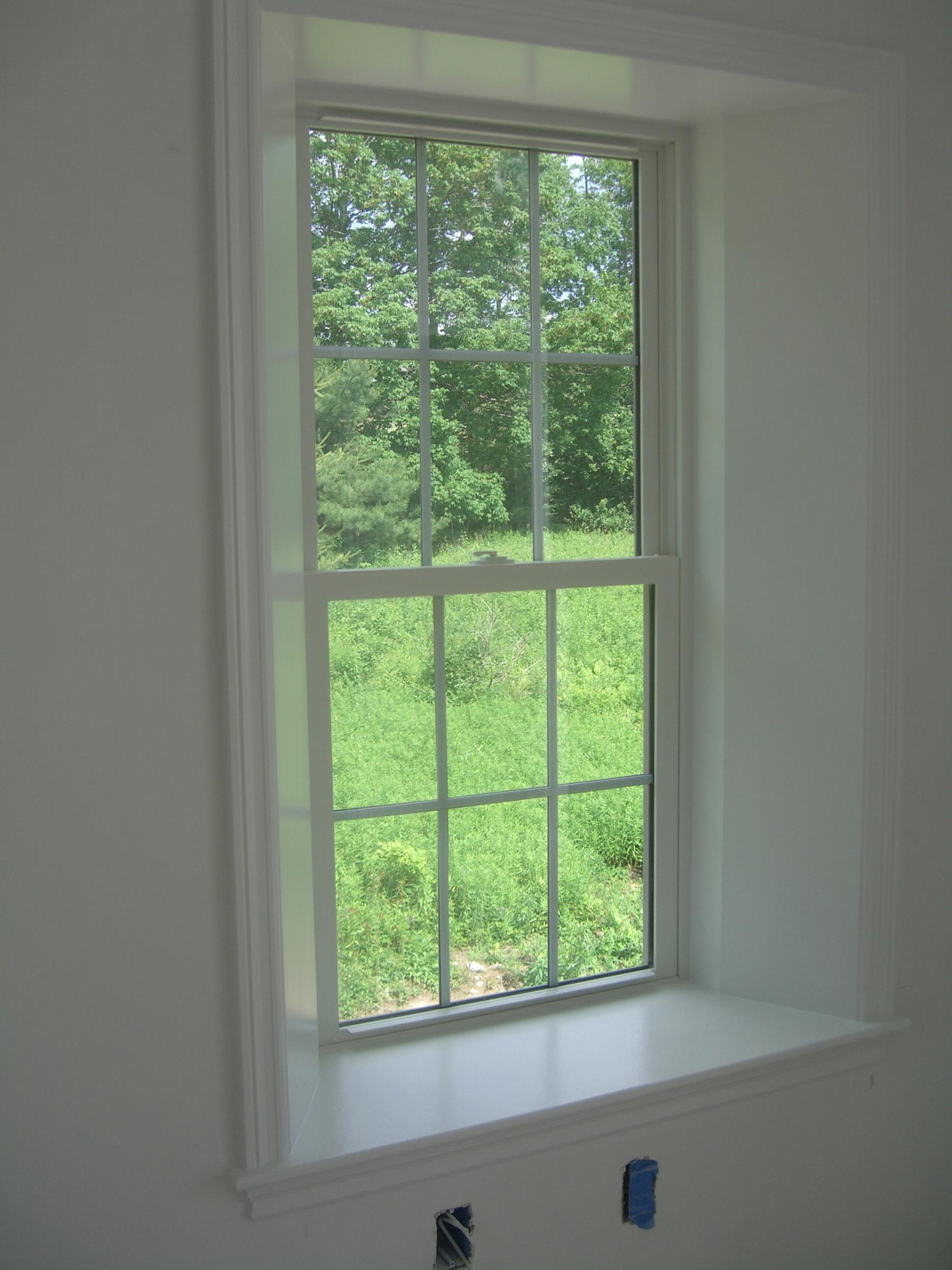
Site conditions:
Renewable Energy Sources:
Window Description:
Windows U-value of 0.20, SHGC of 0.23.