Project Subtitle:
Project Description:
A research, development, test and evaluation single-family residential project to determine the suitability of the International Passivhaus standard for the North American market. North American concepts such as Optimum Value Engineering (OVE) and the Larsen truss system were melded with Passivhaus performance criteria resulting in a relatively easy to produce and replicatable building. In fact, this internationally pre-certified project was constructed almost entirely by a single person with no prior building experience over a two year time span. During preliminary blower door testing infiltration rate was approximately half that allowed by the Passivhaus standard. Final blower door testing and subsequent International Passivhaus certification is forthcoming in the not too distant future. Overall, the most significant impediments to project execution came not from material limitations but intellectual and performance limitations of ancillary parties.
Building Type Summary:
Address:
Elevation:
Lat. / Long.:
Location Type:
Köppen Climate Type:
Climate Region:
Solar Insolation:
Annual HDD :
Annual CDD:
HDD Base Temp:
CDD Base Temp:
Occupancy Type and Details:
Owner-occupied. 2 full-time occupants. 70 hours at the building per week.
Conditioned Floor Area:
Conditioned Building Volume:
Multiple buildings?:
Total floor area of project (all buildings):
Historic?:
Completion date:
Site description:
Four acre wooded site with significant elevation and ledge features located in Portland, Maine. Woods dominated by deciduous trees. A few mature pines interspersed to the southeast. Building's axis was shifted 15 degrees west of south to enhance winter heating.
Materials:
Project addresses all issues above through the minimization of building size. A deliberate effort was made to create as compact a building as possible without occupants feeling encroached upon. An open floor plan was utilized on the first floor with linked passages and sight lines on the second to create synthetic space out of limited physical space.
Project utilized Optimum Value Engineering principles to reduce material use and thermal bridging related energy loss. Foam was used for sub-slab insulation, otherwise insulation was comprised of mineral wool and cellulose.
Energy Highlights:
The point of the project is to make use of no unusual energy strategies in this all electric design. Sound design eliminated the need for novel complexity although advanced appliance components were utilized to maximize the efficient use of energy in concert with Passivhaus requirements. For example, a ducted heat pump water heater was used to increase the efficiency of water heating. Additionally, a heat pump dryer was used to bypass the requirement for a dryer vent that typically makes achieving Passivhaus air tightness unnecessarily complex. The range uses induction technology for cooking with a recirculating range hood providing filtering of effluent prior to evacuation by the HRV system.
LCA Description:
No.
Electric Utility Company:
Datasets and Utility Bills sources and reliability:
Central Maine Power. Utility grade.
Energy Storage type:
A small amount of insulated thermal mass consistent with North American light residential construction.
Subslab assembly:
Legalett system using 8" EPS.
Slab edge assembly:
Legalett system using 4" EPS
Foundation wall assembly:
None.
Above grade wall assembly:
2x6 24 on-center load bearing wall assembly.
11 7/8" I-joist based Larsen assembly.
Flat attic assembly:
30" raised-heel truss assembly.
24" loose fill cellulose.
Door Area:
Space heating - Manufacturer & Model:
Space heating - capacity:
Space cooling - Manufacturer & Model:
Domestic hot water - Manufacturer & Model:
Domestic hot water - capacity:
Domestic hot water - efficiency:
Ventilation - Manufacturer & Model:
Process:
The design process was iterative using a combination of 3D modeling with SketchUp to determine feasibility coupled with the PassivHaus Planning Package to ensure performance. Guidelines used during the process follow.
2' module governed structural dimensions.
2 story to reduce building footprint.
Open floor plan concept.
Area of fenestration minimized to that necessary to provide Passivhaus energy performance levels.
Eliminate unnecessary use of enclosed space.
Design for Adaptability:
Floor and roof system are trussed resulting in clear spans on each floor of the two floor building. Reconfiguration is possible without disturbance of the high performance building envelope.
Other Software tools:
SketchUp
Energy Modeling Software:
2007 PassivHaus Planning Package.
Outcome of project goals:
Design and build a Passivhaus - achieved. Hard work by participants, YouTube, and the availability of information via the internet.
Use Air Admittance Valves - failed. City of Portland would not accept licensed engineer's documents.
Discrepancies:
TBD.
Finances Description:
Self financed drove a minimization of cost through a minimization of the size of the building.
Total Cost of Project:
Construction hard cost:
Gross Cost of Renewable Energy System:
Value of Tax Credits for renewable energy systems:
Net Cost of renewable energy systems:
Federal incentives:
None.
State incentives:
$500 heat pump water heater rebate.
Local incentives:
None.
Utility incentives:
None.
Other incentives:
Personal achievement.
Advice:
High performance costs more. Simplicity is a complexity all its own. Stay true to the intent of the design.
Special architectural measures:
See Passivhaus design requirements.
Energy Strategies:
Replace typical heating system with the sun by designing and building to the International Passivhaus standard. Minimize electricity consumption by incorporating state of the art Energy Star rated components.
Energy Use and Production Documentation:
Subslab R-value:
Slab edge R-value:
Above grade wall R-value:
Flat attic R-value:
Average window U-factor:
Solar Heat Gain Coefficient:
Visible Light Transmittance:
Door U-Factor:
Cost per square foot of Conditioned Space:
Air Changes per hour, ACH50:
Project Photos:
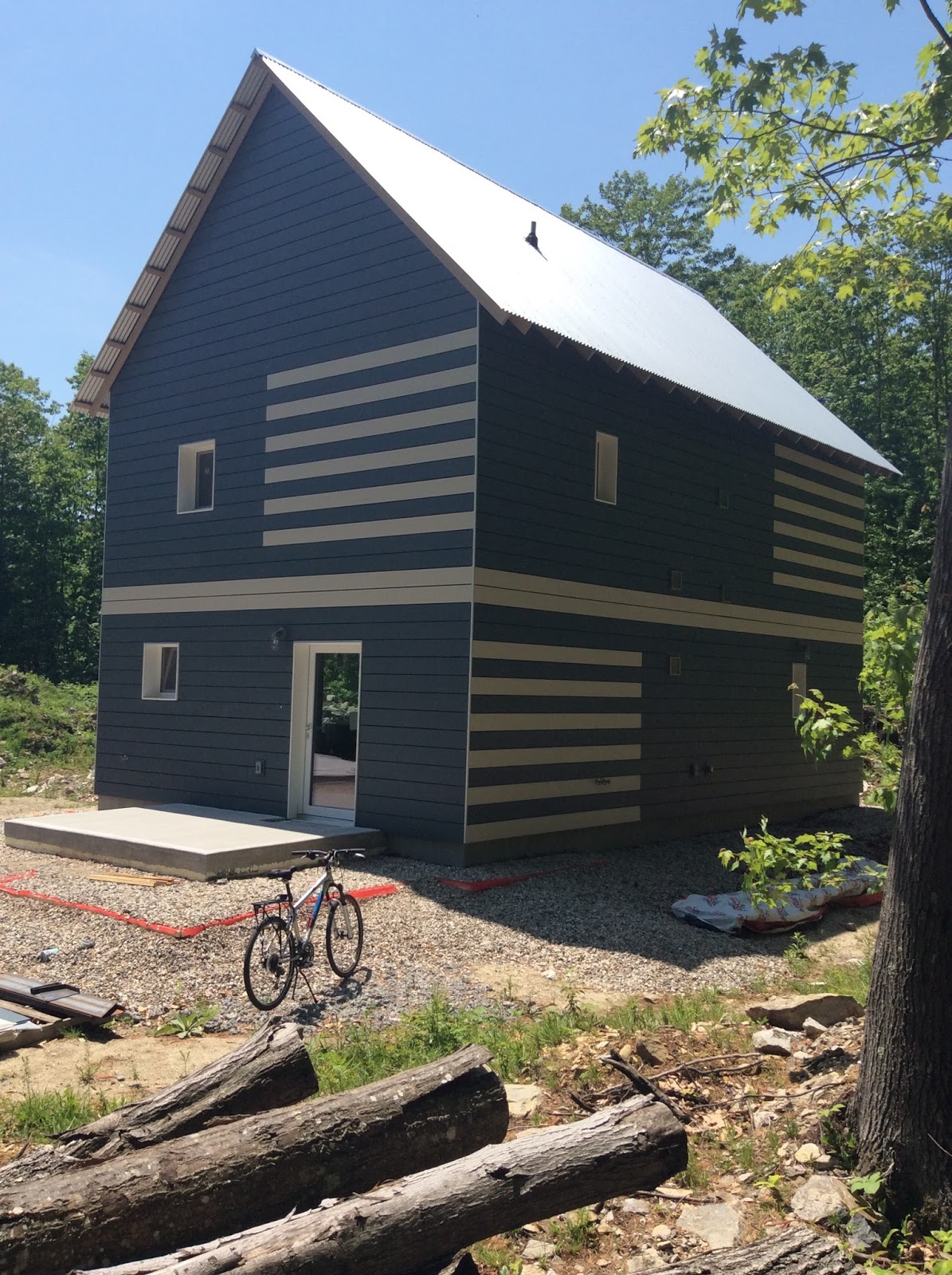
Number of Bathrooms:
Scope Description:
Single-family residential with intent for part time utilization of in-home office.
Site conditions:
Other Purchased Fuels Description:
No.
Summary of enclosure strategy/description:
Foundation - Frost Protected Shallow Foundation (FPSF).
Wall - 2x6 load bearing / 11 7/8" modified Larsen truss system utilizing I-joists. Mineral wood insulation.
Floor - Floor truss system.
Roof - Raised heel truss system. Loose fill cellulose insulation.
Air barrier - 1/2" plywood.
Window Description:
Schuco SI82.
Door Description:
Schuco SI82
Number of Bedrooms:
Team Members:
Architect - Karen Bala (Dyer Brown)
Mechanical Engineer / Energy Consultant - Sonia Barrantes (Ripcord Engineering)
Civil Engineer / Mechanical Engineer / Electrical Engineer / Sprinkler Designer / Energy Consultant / 3D Designer / Builder / HVAC Installer / Electrical System Installer / Sprinkler System Installer / Landscape Designer / Air Sealing / Insulation / ETC - Jake Staub (Ripcord Engineering)
Excavation - Jeff Munn (Coastal Construction Services)
Concrete Work - John Michaud (Michaud Concrete Works)
Electrical Service Installation - Bob Bauman (Bauman Electric)
Mechanical Equipment Installation Details and Comments:
Blower door test to Passivhaus standards.