Project Subtitle:
Project Description:
This is a new house in the Katywil Farm Community, an intentional cohousing community in Colrain Massachusetts. It was designed as a Net-Zero house by the owner/architect Peter Brooks after taking Marc Rosenbaum's first NetZero design course. It is derived from the Capstone project from that course. The house was built by Karsten Construction of Leverett. We have a heated walk-out basement that is unfinished but has a radiant slab floor and an unheated root cellar room. The house is a 26 x 34' rectangle with a secound floor that has shed dormers on the North and South sides. The house is sited facing slightly East of South on a South facing slope. It is designed with about 8% south facing triple glazed windows and small windows on the north. The walls are double studded 12" thick packed with dense cellulose. The roof was designed to have 18" of cellulose, about R60. The house was built quite tightly and tested at .8 ACH50. The house is ventilated by a Fantech Flex 100 ERV. The house is heated by a Daikin air to water heat pump that pumps hot water to the DWH indirect tank and the radiant slab and radiators. There is a 7.6 kW solar PV array of 30 panels, with half on the 45 degree sloped roof and half of the panels are on the top of the dormer roof at about 30 degrees.
We have just received 12 full months of energy data and we seem to have generated enough power to be within 12% of NetZero. We need to generate an extra 671 kWh to offset the 24 gallons of propane that we used for cooking. We will add a monitoring to the system and refine our use until we meet our goal of Net-Zero.
Building Type Summary:
Address:
Elevation:
Lat. / Long.:
Location Type:
Köppen Climate Type:
Climate Region:
Solar Insolation:
Annual HDD :
Annual CDD:
HDD Base Temp:
CDD Base Temp:
Occupancy Type and Details:
Owner occupied
Conditioned Floor Area:
Conditioned Building Volume:
Semiconditioned Floor Area:
Unconditioned Floor Area:
Multiple buildings?:
Total number of units in project (all buildings):
Total floor area of project (all buildings):
Historic?:
Completion date:
Site description:
The site is a southerly sloping field in a planned unit development on an abandoned apple orchard.
Materials:
This house is a wood frame structure incorporating Zip sheathing and Advantech building products. Modern framing techniques were used. The house is clad with Hardie siding. The roofing is Fabral steel roofing. The flooring is bamboo throughout with linoleum used in the kitchen and bath. The interior trim is all local knotty pine. All lighting fixtures and some cabinetry were purchased from the Restore and the Eco Building Store in Springfield.
Energy Highlights:
This is a super-insulated, passive solar house with a 7.6 kW solar PV system. The heating and DHW is by a Daikin Altherma heat pump system supplying hot water to a radiant slab and radiators. The heat pump is rated to have a COP of over 4.0.
LCA Description:
Only long lasting products like the metal roofing and Hardie siding were used in this house.
HERS Index:
Annual renewable energy generated:
Electric Utility Company:
Gas Utility Company:
Datasets and Utility Bills sources and reliability:
Eversource.
Electricity amount (imported from grid):
Electricity amount (credited or exported to grid):
Net electricity usage (purchased electricity):
Natural gas amount (purchased energy):
Energy Storage type:
NA
CHP System Description:
NA
Subslab assembly:
We have two layers of 2" extruded polyurethane under the slab, R20,with a vaor barrier and 6" of crushed stone.
Slab edge assembly:
The slab edge is separated from the foundation by 2" of polyurethane insulation ~ R10.
Foundation wall assembly:
The below grade foundation is an 8" concrete wall with waterproofing. It is insulated on the inside with 2" of polyurethane insulation and a stud wall with blown in dense packed cellulose and 1/2" gypsum board for a total nominal R value of 22.
Above grade wall assembly:
The above grade walls are 12" double studded walls with dense packed cellulose between zip sheathing and 1/2" gypsum board. The band joist is sprayed with 8" of closed cell foam. The air and water barriers are taped zip sheathing.
Flat attic assembly:
The flat ceiling areas have approximately 16" of lose blown cellulose insulation. The roof is plywood sheathing with a ceiling of taped zip sheathing for the air barrier covered with gypsum board.
Cathedral ceiling assembly:
The cathedral ceiling area over the bedroom and bathroom are furred down from the rafters to allow for a vented roof and 18" of dense packed cellulose. The roof is sheathed with plywood and the ceiling is taped zip sheathing as an air barrier covered with pine boards.
Door Area:
Space heating - Manufacturer & Model:
Space heating - capacity:
Space cooling - Manufacturer & Model:
Domestic hot water - Manufacturer & Model:
Domestic hot water - capacity:
Domestic hot water - efficiency:
Ventilation - Manufacturer & Model:
Process:
As an experienced architect with much extra training in low energy buildings, my challenge was to fit my concept from my NESEA NetZero design course onto this site and accommodate all my partner Kaylee's needs. I took Mark Rosenbaum's first NetZero design course and developed a plan for northern NH. Later we bought a lot in Western Massachusetts. The house is similar but here it faces south while the lot slopes to the east. We have a walk-out basement, very useful for accommodating all our gardening needs. The basement includes a very important underground, thermally separate root cellar under our unheated Mud Room. The Mud Room is adjacent to the unheated garage which has a steep trussed roof with attic storage.
We have used local knotty pine trim throughout the house, the floors are bamboo and linoleum in the kitchen and baths. All the lighting fixtures the are not recessed are reused from the Restore or Eco-Building supply of Springfield.
Design for Adaptability:
The house was designed for aging in place and also to keep costs manageable. We have a flexible space on the first floor that can be converted to a bedroom in the future and now serves as a guest room. There is an adjacent bathroom with an accessible shower. All the first floor doors are wheel chair accessible.
The front door and adjacent deck can easily be ramped if needed.
Energy Modeling Software:
The house was modeled with Marc Rosenbaum's modeling spreadsheet for predicting the PV system requirements to meet Net Zero. In order to predict the PV needed to reach net zero the program calculates the solar heat gain, the peak heat load and power required to heat the hot water.
Outcome of project goals:
All design is a question of making the best compromises to reach the goals. We did a number of things which are compromises in energy efficiency to make a very pleasing and livable house. We have too many decks and doors and windows. The upper deck off the second floor was designed as a place to dry laundry and it works very well, we have no electric drier. The extra kitchen door is very handy for garden and compost access. The lower porch is great for shaded eating in the summer and wood storage in winter.
Our heat pump system has performed well over the first hard winter. It certainly seems to run continuously and only makes warm water in the sub-zero temps. That's when the wood stove helps out.
All out project goals have been met. With one exception. We installed PV panels on the dormer roof (27 degrees) and on the garage roof (45 degrees). I found that the low slope panels, while a good slope for the summer sun, were snow covered for at least two winter months. Not something we can change now. The houses that I've designed subsequently have uninterrupted 10/12 pitch roofs on the south side.
Discrepancies:
Marc's model predicted that we would be Net Zero with a 6.7 kW system. Our predicted peak load was under 8,000 BTU/hr. We under estimated our electric loads despite picking the most efficient appliances available. During our first year we used over 12,000 kWh, now we will install a monitoring system to try and understand that. We did irrigate a lot in the summer to grow food.
The heat pump has worked well, though it may consume more power than predicted. We may install more radiators to extract more heat from the same power input.The smallest heat pump system that Daikin made was 18000 BTUs with a cop of 4.6 which seems unreasonable. At -5 degrees F it is probably only half of that. We installed piping for extra radiators if we feel they are needed. We only have one radiator on each floor and they do the job. Our roof could fit 30 panels without shading so that's what was installed.
We need to encourage more manufacturers to bring their air to water heat pump systems to the US as soon as possible!
Finances Description:
This is a dream house on a budget. Kaylee and I are mostly retired now. We call this our last big adventure, a new house for a new relationship. To meet the dream we can't compromise too much. It would not have been possible without doing well selling my house in Watertown MA which was an Arts & Crafts bungalow that I had renovated.
Total Cost of Project:
Construction hard cost:
Gross Cost of Renewable Energy System:
Value of Tax Credits for renewable energy systems:
Net Cost of renewable energy systems:
Federal incentives:
30% tax credit of qualified expenditures.
State incentives:
Solar 2 rebate $3250.
Massachusetts maximum tax credit of $1000.
Tier 3 rebate of $7,000
Local incentives:
NA
Annual Electric Savings:
Annual Revenue from SRECs or other renewable energy credits:
Special architectural measures:
This house is highly insulated and tightly built. It is design to take advantage of the solar heat gain with southern glass equal to about 8% of the floor area. The windows are triple glazed local PVC framed windows with a relatively good SHGC. The house has a 2' roof over hang on the Southern side to shade the windows from the high summer sun. The basement is open to the rest of the house and is mostly below grade. The root cellar is thermally separate from the basement by an R 10 slab break and R 42 wall insulation.
Energy Strategies:
We designed our house to reduce the heat lose and maximize the heat gain without over heating and then add solar PV to power our efficient heat pump system. We do have a small wood stove to use for extended below zero weather.
Energy Use and Production Documentation:
Subslab R-value:
Slab edge R-value:
Foundation wall R-value:
Above grade wall R-value:
Flat attic R-value:
Cathedral ceiling R-value:
Average window U-factor:
Solar Heat Gain Coefficient:
Visible Light Transmittance:
Door U-Factor:
Cost per square foot of Conditioned Space:
Project Photos:
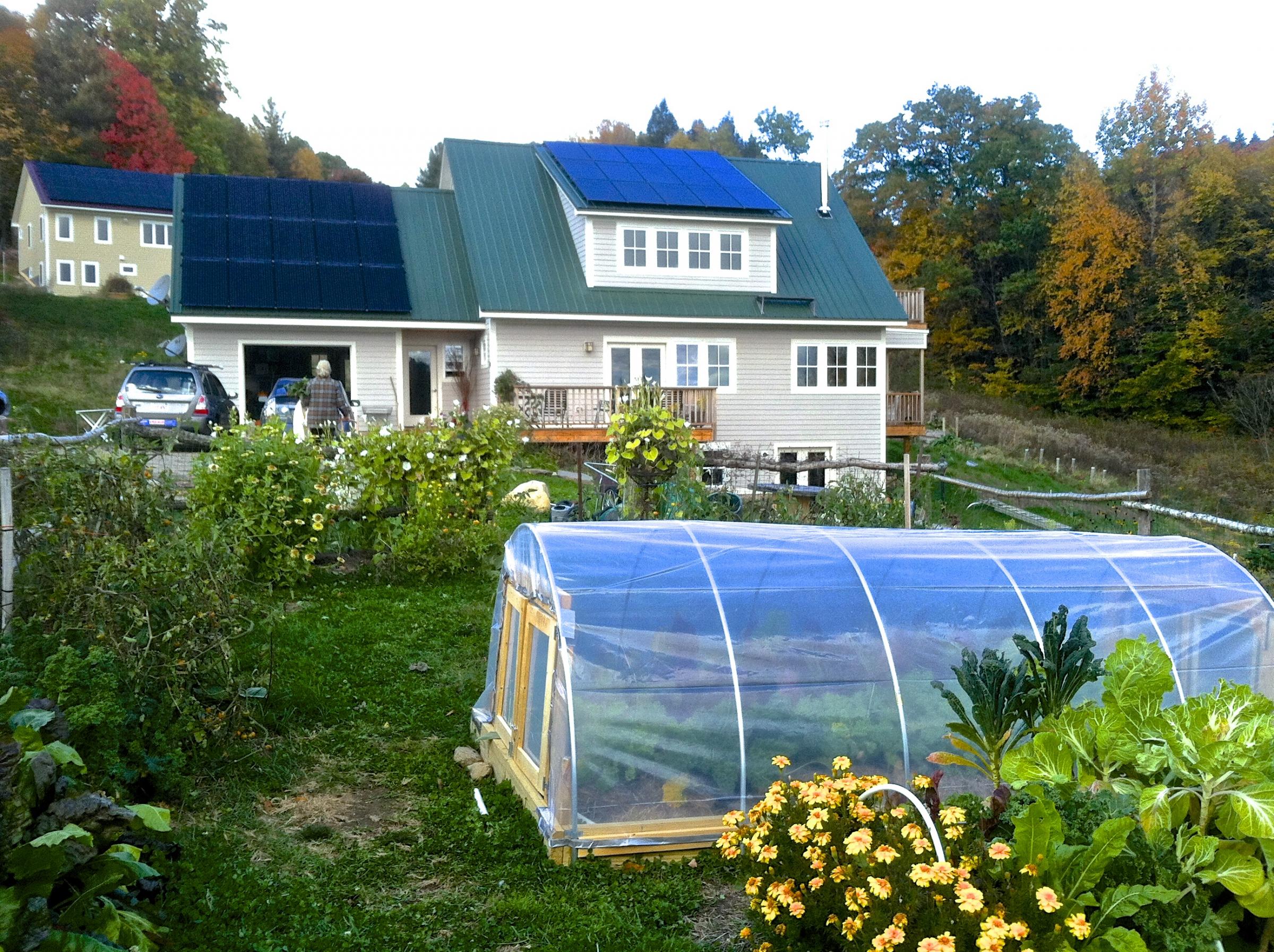
Number of Bathrooms:
Scope Description:
Totally new construction. The heated area is approximately 2200 SF.
Site conditions:
Renewable Energy Sources:
Other Purchased Fuels Description:
No
Summary of enclosure strategy/description:
The house is two stories with a walk-out basement. Our bedroom is upstairs under a shed dormer. Our utilities and root celar are in an unfinished basement.
Walls are 12" double studded with dense packed cellulose insulation, R42. The roof has 18" of cellulose insulation, R60.
Roof Assembly:
The rood insulation is described under the flat attic and cathedral ceiling sections. All roof sections are covered with 1/2" plywood sheathing, a roofing underlayment membrane and metal roofing. The roof is a vented assembly with peak and soffit vents.
Roof R-value:
Window Description:
All the windows are PVC framed casement windows made by Mathews Brothers of Maine since 1854.These are the Clara Starett high performance triple glazed windows with foam insulation in the PVC frames. The glazing is called the PassivGlas-Plus package with 1" triple pane glass with two surfaces of low-e coatings (8070) with argon gas.
Door Description:
Fiberglass with wood edges, Therma-tru, smoothstar.