Project Description:
Holland Passive House, located on the eastern shore of Lake Tashmoo on the island of Martha’s Vineyard, is a two story, wood framed, single-family residence designed to be certified to the Passive House Standard. The siting, general layout and orientation of the home have been established to maximize the effect of natural day-lighting and create a sense of privacy from neighboring properties while providing dramatic views to Lake Tashmoo beyond. The home features natural, low maintenance exterior finishes and contains no combustion equipment. Primary strategies employed to reach ZNEB requirements include load reduction (meeting and exceeding the air-tightness and thermal requirements of the Passive House standard), minimal electrical usage in conjunction with roof mounted PV and solar domestic hot water systems. Large glazed west façade areas provide a spectacular view of Lake Tashmoo, while the covered ‘porch’ areas on the West façade help mitigate unwanted solar gains during the summer months.
Building Type Summary:
Other Awards:
In 2016, this building was awarded a $10K grant as a Zero Net Energy Building under the Pathways to Zero Net Energy Program administered under by the Massachusetts Executive Office of Energy and Environmental Affairs (http://www.mass.gov/eea/energy-utilities-clean-tech/energy-efficiency/ze...).
Address:
Elevation:
Lat. / Long.:
Location Type:
Köppen Climate Type:
Climate Region:
Solar Insolation:
Annual HDD :
Annual CDD:
HDD Base Temp:
CDD Base Temp:
Occupancy Type and Details:
Owner Occupied - Full time occupancy in the summer months, 2-3 days/wk during the off season.
Conditioned Floor Area:
Conditioned Building Volume:
Multiple buildings?:
Total floor area of project (all buildings):
Historic?:
Completion date:
Site description:
Situated on a long narrow site, the residence was designed to carefully consider the impact the building will have on the site & the neighboring properties all while enhancing the privacy of the property and the home. Through the development of a master plan for the property, site strategies and building forms maximize natural light and views to Lake Tashmoo and beyond. Passive solar strategies together with careful consideration of coastal/prevailing winds minimize the impact on the natural environment (by reducing the need for energy consumption) and will provide utmost comfort during all seasons.
Materials:
All Framing at 24" O.C.
Natural Alaskan yellow cedar siding & trim.
FSC certified hardwood decking.
Insulation was carefully selected to minimize environmental impact, including the use of cellulose, spray foam insulation with water based blowing agents, and plastic foams with blowing agents that have low Greenhouse Gas Warming Potential, such as EPS and Polyisocyanurate.
The design and installation of an advanced treatment (de-nitrifying) septic system further promotes a healthy and environmentally sensitive approach to home building.
Energy Highlights:
Design to the Passive House standard carefully examines all energy uses, and must aggressively manage them to achieve Passive House certification for a small building in a cold climate like this one. So aggressive passive design techniques are used to minimize annual energy use, at a higher first cost in design and materials and this minimizes the need for additional energy sources, maximizes the return delivered by the PV and solar DHW systems, and the ground loop ventilation pre-conditioning system. The slab on grade is significant in moderating temperature fluctuations, by absorbing and re-radiating solar energy. Shading via South elevation brise soleil and deep West porch overhangs help manage unwanted gains in conjunction with operable internal shading.
HERS Index:
Annual renewable energy generated:
Electric Utility Company:
Gas Utility Company:
Datasets and Utility Bills sources and reliability:
Source is utility bills and PV meter readings (for SREC program).
Natural gas amount (purchased energy):
Energy Storage type:
The superinsulated slab on grade absorbs solar energy entering via the South glazing, managed by the brise soleil.
Two 80 gal. solar DHW tanks store solar energy from the 93 sf flat plate solar collectors array.
Subslab assembly:
- 4" Reinforced Poured in Place Concrete Slab on Grade
- 10 Mil. Poly Vapor Barrier - Continuous Under Entire Slab & Over FND Wall, Wrapped/Taped Up Exterior Side Wall (All Seams Taped)
- 12" EPS Type II Insulation Under Entire Slab And At All Slab Edges
- Compacted Backfill
Slab edge assembly:
- 4.75" EPS Type II Insulation
Foundation wall assembly:
- Damp Proofing to Grade
- 8" Reinforced Poured in Place Concrete Foundation Wall Over Continuous Concrete Footing
Above grade wall assembly:
East/West Wall Assembly:
- Yellow Cedar Shingles (Max 5" Exposure)
- 2 Layers Of #15 Felt
- 1/2" 'Zipwall' OSB Sheathing (All Seams & Joints Taped)
- Acoustical Sealant at All Wood to Wood Connections, Typ
- 2x4 Spf (Spruce Pine Fir) Framing Spaced 24" O.C. Filled W/ High Density Closed Cell Spray Foam
Insulation
- 2 1/4" Cavity Filled W/ High Density Closed Cell Spray Foam Insulation
- 2x4 Spf (Spruce Pine Fir) Interior Framing Spaced 24" O.C. Filled W/ High Density Closed Cell Spray Foam Insulation
- 1/2" Gwb W/ Skim Coat of Plaster, Painted
North/South Wall Assembly:
- Yellow Cedar Shingles (Max 5" Exposure) @ Sidewalls, 1x4 Vertical Yellow Cedar at Window
Groupings, & 1x6 Yellow Cedar Shiplap Siding @ 1st Floor Powder Room - East Wall
- 2 Layers Of #15 Felt (Second Layer Interwoven W/ Shingles Every Six Courses)
- 1/2" 'Zipwall' OSB Sheathing (All Seams & Joints Taped)
- Acoustical Sealant at All Wood to Wood Connections, Typ.
- 2x6 Spf (Spruce Pine Fir) Framing Spaced 24" O.C. W/ 4" High Density Closed Cell Spray Foam Insulation & 1 1/2" Dense Pack Cellulose Insulation
- 7 1/4" Cavity Filled W/ Dense Pack Cellulose Insulation
- 2x4 Spf (Spruce Pine Fir) Interior Framing Spaced 24" O.C. Filled W/ Dense Pack Cellulose Insulation
- 1/2" Gwb W/ Skim Coat of Plaster, Painted
Flat attic assembly:
Roof Assembly - Flat Roof:
- Kemper Drainage Plane/Roofing System
- 1/2" Plywood
- Tapered Polyiso Insulation, Min. 1/8" Per Ft. (Max. Thickness = 4 11/16", Min. Thickness = 1/2")
- (3) 2" Layers of Poly Iso Insulation Over Entire Roof
- 5/8" 'Zipwall' OSB Roof Sheathing; All Seams & Joints Taped
- 14" J14 Trimjoist Open Web Structural Roof Framing Spaced 24" O.C. Filled W/ Dense Pack Cellulose Insulation
- 1x4 Spf (Spruce Pine Fir) Strapping
- 1/2" Gwb W/ Skim Coat of Plaster, Painted
Cathedral ceiling assembly:
Roof Assembly - Pitched Roof:
- Asphalt Shingles
- Ice & Water Shield Over Entire Roof & Turned Down @ All Wall-To-Roof Connections (Min. 1'-0")
- 1/2" Cdx Plywood
- (3) 2" Layers of Poly Iso Insulation Over Entire Roof
- 5/8" 'Zipwall' Osb Roof Sheathing; All Seams & Joints Taped
- Acoustical Sealant at All Wood to Wood Connections, Typ
- 16" Tji 210 Structural Roof Framing Spaced 24" O.C. Filled W/ Dense Pack Cellulose Insulation
- 1x4 Spf (Spruce Pine Fir) Strapping
- 1/2" Gwb W/ Skim Coat of Plaster, Painted
Door Area:
Space heating - Manufacturer & Model:
Space heating - capacity:
Space cooling - Manufacturer & Model:
Space cooling - capacity:
Domestic hot water - Manufacturer & Model:
Domestic hot water - capacity:
Domestic hot water - efficiency:
Ventilation - Manufacturer & Model:
Process:
It was clear early in the design process that Passive House Certification was a primary goal for the project team and owners. As such, the Hollands & Hutker Architects attended a four (4) hour workshop facilitated by Mike Duclos at the 2014 JLC Live Conference in Providence, RI to ensure an understanding of the considerable challenges and significance of a Passive House project. This event was a wonderful team building exercise and provided the encouragement and inspiration to move the project forward and engage the remainder of the primary project team, including Mike Duclos of DEAP Energy Group and Energy Efficiency Associates. Mike Duclos, the Certified Passive House Consultant responsible for the energy design features, testing, remediation and commissioning of the Falmouth Passive House, the second certified in Massachusetts, worked closely with Hutker Architects during the design development phase, evaluating performance trade-offs in all major building assemblies, assessing mechanical system options and specifying the renewable energy strategies (in that order) to optimize the ‘house as a system’ design. Mike provided the Hutker Architects with a custom UA based spreadsheet calculator for conducted heat loss calculations to facilitate the selection and quantification of insulation for various building assemblies, by facilitating ‘design space exploration’ of trader-offs among opaque and glazed assemblies, shell performance, and size in the context of a simple heat loss model targeting a reasonable starting point with respect to space heat demand.
Mike Duclos constructed a PHPP model and worked with the Hutker Architects to further refine the starting point in the context of solar gains, shading, ventilation and DHW system layout, etc. to meet the Passive House space heating, cooling and primary energy criteria, with the builder Farley Pedler engaged in the process early on.
Design for Adaptability:
The residence is designed to allow the homeowners to 'age in place', providing flexibility for the first floor family room, to transition into a master suite.
Flat roof portions of the home & garage are designed to provide the opportunity to introduce additional solar arrays, and roof gardens.
The approach of providing the simple UA calculator feedback to the architects is well worth considering for those without extensive PH design experience. This could also be expanded into a 'PHPP Lite' which allows feedback to include solar gains and shading providing an educational opportunity, as well as a design loop iteration and time reduction.
Energy Modeling Software:
Simple custom designed UA calculator
PHPP Version 8.5
REM/Rate
Outcome of project goals:
Certified Passive House (Passive House Academy)
LEED Platinum.
Tier III MA New Construction Program
This is a Mass New Construction Tier III home.
This home was awarded a DOER Zero Net Energy Building grant application.
Zero Net Energy operation remains to be measured.
Discrepancies:
Actual energy use data are not yet available
Finances Description:
The uniqueness of the Passive House construction made it impossible to find a builder on Martha’s Vineyard with the Passive House expertise and willingness to bid on the project on a fixed price contract basis, and so a cost-plus contract was executed with Farley Built, Inc. of Tisbury, Massachusetts, with construction costs in-line with major construction projects on Martha’s Vineyard.
Gross Cost of Renewable Energy System:
Value of Tax Credits for renewable energy systems:
Net Cost of renewable energy systems:
Federal incentives:
Federal Rebate for PV System: $7934
Federal Rebate for SHW System: $4143
State incentives:
MA Residential New Construction Program Tier III incentive: $7K
PON Zero Net Energy Building grant: $10K + $2K for hygrothermal modeling.
MA Income Tax Credit for PV System: $1K
Annual Electric Savings:
Annual Revenue from SRECs or other renewable energy credits:
Special architectural measures:
Designed to meet Passive House standards.
Attention to passive window shading details through the use of brise soleil’s on the south, and deep overhangs on the west, minimize the need for cooling in the warmer months.
Geothermal loop was installed for pre-heat and pre-cool of ventilation air.
Roof mounted PV solar array & solar DHW collectors.
To further strengthen the idea of passive survivability, the Holland House will not rely on a propane generator for power outages, with systems in place to use a hybrid electric car or Wall Battery as a possible backup power generation on site.
Carefully designed storm water management system was installed.
Energy Strategies:
100% Electric home.
Aggressively minimize energy use using passive techniques described above, using super-insulation, thermal bridge free design, ~ R9 / SHGC 0.50 center of glass windows, extremely low air infiltration, high performance ERV with ground loop pre-heating / dehumidification, PV, Solar DHW to meet Passive House space heating, cooling and primary energy requirements.
Subslab R-value:
Slab edge R-value:
Above grade wall R-value:
Flat attic R-value:
Cathedral ceiling R-value:
Average window U-factor:
Solar Heat Gain Coefficient:
Visible Light Transmittance:
Door U-Factor:
Air Changes per hour, ACH50:
Project Photos:



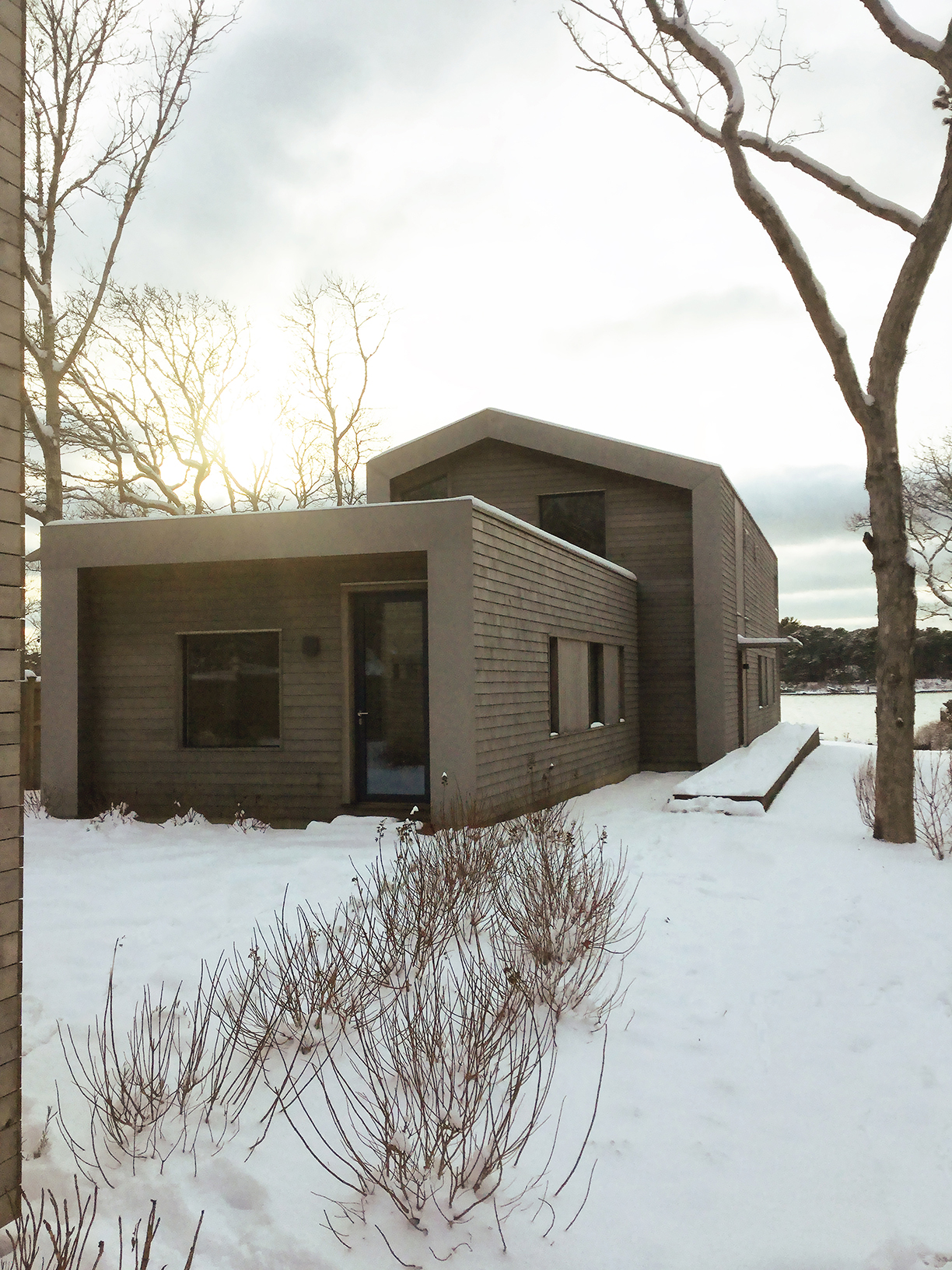

Number of Bathrooms:
Scope Description:
Two story, wood framed, single family residence.
Site conditions:
Renewable Energy Sources:
Other Purchased Fuels Description:
No
Storage Strategies & System Details:
See above.
Summary of enclosure strategy/description:
Passive House super-insulated, air tight envelope designed to meet 4.75 KBTU/sf/yr space heating/cooling demand.
Low U, high SHGC glazing managed by fixed and operable shading.
A super insulated slab on grade to absorb, store and re-radiate solar energy.
A long building axis being near due South, with enhanced glazing area due to compensate for some South tree shading, the impact of which is mitigated by the slab on grade storage mechanism.
Roof Assembly:
See Flat & Cathedral Assemblies
Window Description:
Makrowin MW88 Aluminum Clad Integral Windows with Triple Glazed Low E Climatop Ultra-N Insulated Glass
Center of glass U = 0.11
Door Description:
Makrowin MW88 Aluminum Clad Doors with Triple Glazed Low E Climatop Ultra-N Insulated Glass
Mechanical Equipment Installation Details and Comments:
Air Source Heat Pumps for space heating and cooling have been installed and verified to be operational to manufacturer’s specification by the HVAC installer.
Duct systems for heating and cooling air distribution had their total leakage measured, and they comply with the building code.
The solar DHW System has been installed and verified to be operational by the system installer and has a reporting mechanism to detect if the system has malfunctioned so it can be repaired, to avoid the issue of unconscious excessive DHW backup energy use. The system is expected to serve the majority of annual DHW use, estimated by RESNET criteria as approximately 18250 gallons / year.
The Zehnder hygienic and point source air exchange system has been commissioned by a Zehnder certified commissioning agent, with results outlined in the issued ventilation system commissioning report. The ventilation system has been balanced to within 10% of flow rate at the fresh air / stale air ports to outside to minimize core freeze up potential and maximize heat exchange efficacy. The ventilation system flows in each room have been measured using a moving vane anemometer and adjusted repetitively to insure adequate air extraction and supply as stipulated in the ventilation system plan. Ventilation system power has been measured.
As required by Passive House Institute for final certification, a bidirectional, multipoint blower door test was run using Tectite software to collect data, analyze and graph the results, which were 161 CFM@50 Pa depressurization, 103 CFM@50 Pa depressurization, and PHI/PHA uses the average of these – 132 CFM@50 Pa to compare to the certification criteria of 0.6 ACH@50 Pa.