Project Subtitle:
Project Description:
Originally built in 1858, the house at 11 Poplar Street, had always been a charming farmhouse with perennial allure, welcoming everyone, even when distressed. It will be again.....that is, once it is finished being reincarnated later next year.The property sits in the bucolic village district of Andover, NH. Close enough to the campus of Proctor Academy, and just distant enough from the main road, to be pleasant and convenient. As you exit the main building on the Proctor campus, you'd see just enough of farmhouse, its wrap-around porch and other charming architectural elements, that you couldn't help but travel down to the end of the short road to take a better peek and see just what the whole house had to offer.
The current owners, Brad & Megan Hardie, purchased the property at auction in late 2013. It was purchased in nearly condemnable condition, and was in need of lots of love. Stereotypical of many older farmhouses, the structure was a variation of the "expansion mansion" genre of building, where additional spaces, were just affixed and/or cobbled onto the original farmhouse, one after the other, as the need arose. The annex had most recently been used as a two bedroom apartment and prior to providing additional housing, the extensions housed a graphic design studio, and even operated as a chinchilla ranch at one point! At just under 3/4 of an acre, the property is well proportioned for it's quaint village location, but the arrangement of the affixed structures made the interior of the farmhouse very dark. Removing the spaces that stretched out from the farmhouse, would; enlarge the yard, brighten the interior and invite the rest of yard, located to the west of the house, into the home a bit. Although initially hopeful to salvage, reclaim, recycle and/or upcycle most of the structure, due to typical life, job and of course family time constraints, Brad & Megan decided to demo everything but the original farmhouse. With energetic 4 and 6 year old girls to raise, and based on some advice from a few elders who had taken on similar projects in the past on their own, it has proven to be a wise decision thus far.
Thankfully, in the end, they were able to upcycle quite a bit of the structure to some of their friends, who have since created structures for themselves on their own farmhouse properties. Their goal, after the dust settled from the demo was to do a whole house renovation, square up the footprint of the house, stretch it out a touch, and consequently complete a deep energy retrofit on the remaining farmhouse. Megan who teaches forensics at Proctor Academy, has always been smitten by the property ever since landing in the area over 18 years ago. Brad is who is currently a career firefighter/paramedic has always shared her love for the property. While working in emergency services, Brad has also been building homes and designing projects for over 25 years. Ever since he was a child, he has dreamed of having a fixer upper, or building his own home. They had tried to purchase the house, albeit unsuccessfully, a couple of times over the years, so when the opportunity to purchase the home via auction came up, it just seemed like the right time for a crazy, but wholesome endeavor.
Unfortunately, while demoing the structure, Brad discovered that so much of the remaining farmhouse was found to be rotten, structurally unsound, and/or damaged by a previous fire, that he knocked the whole house down. Fortunately, various elements were salvaged for use later though...
Building Type Summary:
Address:
Elevation:
Lat. / Long.:
Location Type:
Köppen Climate Type:
Climate Region:
Solar Insolation:
Annual HDD :
Annual CDD:
HDD Base Temp:
CDD Base Temp:
Occupancy Type and Details:
Owner Occupied, with In-Law apartment above barn.
Typical full time occupants in home = 4 + dog
Typical full time occupant for apartment = 2 + dog (assumed)
Conditioned Floor Area:
Conditioned Building Volume:
Semiconditioned Floor Area:
Multiple buildings?:
Total number of units in project (all buildings):
Total floor area of project (all buildings):
Historic?:
Completion date:
Site description:
Site previously had a house, attached two bedroom apartment, and additional structure attached, but since been demoed.
Materials:
Reclaimed insulation (EPS) is the primary insulation medium for the entire project. Materials that did not require lots of abatement and were in good serviceable condition were salvaged from the demo of the previously existing structure. Materials were also upcycled to other nearby locations for reuse in other homes. Lead municipal water line was replaced. Reclaimed flooring is used. Locally sourced wood, and planking is to be used whenever possible. Fill and additional loam was sourced just a 1/4 mile from project. Vegetation, flowers and groundcover was/will be transplanted from large project less than 1/8 mile away.
Energy Highlights:
18.55 kW PV. DWHR unit for water. Automation systems will be used when possible. Other than generator and outside grill, no fossil fuel will be used to heat, cool, cook, or heat water on site. Ground loop for HRV.
LCA Description:
When possible, products were chosen with regard to LCA data available via online. There was not an overall LCA performed on the project. Locally sourcing materials, and using reclaimed products like EPS which have a higher Life Cycle Energy Embodiment were chosen in as many situations as possible,
HERS Index:
Annual renewable energy generated:
Electric Utility Company:
Gas Utility Company:
Subslab assembly:
Two layers of 2.75" EPS, offset overlaps. Stego vapor barrier, mastic, tape sealed.
Slab edge assembly:
Nudura ICF, with additional layer of 2.75" EPS to interior and overlap of sub slab EPS, to prevent thermal bridging.
Foundation wall assembly:
Waterproofing membrane, ICF Nudura block, with additional 2.75" EPS to interior. 2x4, and drywall to interior.
Above grade wall assembly:
Siding, 1/2" minimum rainscreen strapping, one layer of 3.25" EPS, two layers of 2.75" EPS, seams offset, sealed, taped, liquid applied air barrier, OSB, blown-in cellulose, drywall
Cathedral ceiling assembly:
standing seam, 5/8" plywood, cold roof vent, supplemental rafter/cold roof, 6 layers of 2.75 EPS, Vapor barrier, 1/2" OSB, barnboard strip sheathing (exposed to interior), exposed rafters.
Space heating - Manufacturer & Model:
Domestic hot water - Manufacturer & Model:
Domestic hot water - capacity:
Ventilation - Manufacturer & Model:
Process:
Lengthy! Overwhelming! Suffocating! Exciting! Educational! Fatiguing! Make it stop.........!!!!! Version after version after version, blah, blah, blah. We have been designing for three years! It was driven by our intent to keep the farmhouse, and complete a whole house, deep-energy retrofit and renovation. In the end even though we didn't save the structure, we kept the design, because we loved the charisma and aesthetic of the original farmhouse.
Design for Adaptability:
Currently the ICF foundation extends beyond the footprint of the main structure, all the way to the outside edge of one side of the farmer's porch and houses the bulkhead underneath. The porch lifts up and exposes the bulkhead, which in New England provides access during the winter, and allowed the house to sit a bit closer to the lot line without encroaching on the setback. If the house ever needs an expansion to allow for a first floor bedroom renovation it will be easily added, because of the ICF foundation wall that supports the outside edge of the porch.
Other Software tools:
SketchUP Pro 6, 7, 8 - seems like every version!
Energy Modeling Software:
Marc Rosenbaum - Proprietary, PVWatts,
Outcome of project goals:
Unknown - to be determined
Discrepancies:
Unknown - to be determined
Finances Description:
Sourcing products locally, that are locally derived, proved to be extremely helpful thus far. Asking questions, and insatiably searching and uncovering products sources, sometimes directly to the manufacturer, until I found the answers I wanted also proved extremely beneficial. Relationships within the building business are vital. I bartered and traded lots of work t make it economically feasible. Sourcing reclaimed material, and relationships that allowed me to get almost 80% of my project materials at lower costs, has made the project feasible. Do It Yourself - Having thorough experience building high quality homes, and designing buildings will also prove to be my lucrative asset.
Total Cost of Project:
Gross Cost of Renewable Energy System:
Value of Tax Credits for renewable energy systems:
Net Cost of renewable energy systems:
Federal incentives:
30% tax credit for PV solar
Energy Star Rebate = $4,000
State incentives:
PUC rebate for PV = $1850
Local incentives:
PV System is not included in tax assessment of property.
Utility incentives:
NH Electric Cooperative =
Rebate for Heat Pump Water Heater = $600
Rebate Energy Audit
Rebate for Mini-Split Heat Pumps = $500/ton max 5 tons ($2500) + $250/ton for whole house heating =$4000 total
Rebate for Wi-Fi Thermostat = $100
Annual Electric Savings:
Annual Revenue from SRECs or other renewable energy credits:
Advice:
Where do I start? To begin with, don't be afraid to ask suppliers and builders to sharpen their pencils. Keep thorough records. Construction loans for owner/builders are one of the hardest, most comprehensive, tiring, stressful processes I have ever endeavored on.
Save, save, save.
Craigslist.
Auctions.
Barter.
Special architectural measures:
REMOTE/PERSIST Technique is used as the primary insulation and air sealing strategy. Window glazing optimization, over hang optimization, wall/window ratio optimization.
Energy Strategies:
All electric, no fossil fuel, LED, Heat pump dryer, heat pump water heater, DWHR, recirculating hot water, ground loop HRV, mini-split heat pump, back up radiant electric, triple pane windows, high efficient HRV/ERV, occupancy sensors, Induction stove, super insulation.
Zero Net Energy definition is not defined as of yet.
Energy Use and Production Documentation:
Subslab R-value:
Slab edge R-value:
Foundation wall R-value:
Above grade wall R-value:
Cathedral ceiling R-value:
Average window U-factor:
Solar Heat Gain Coefficient:
Air Changes per hour, ACH50:
Project Photos:



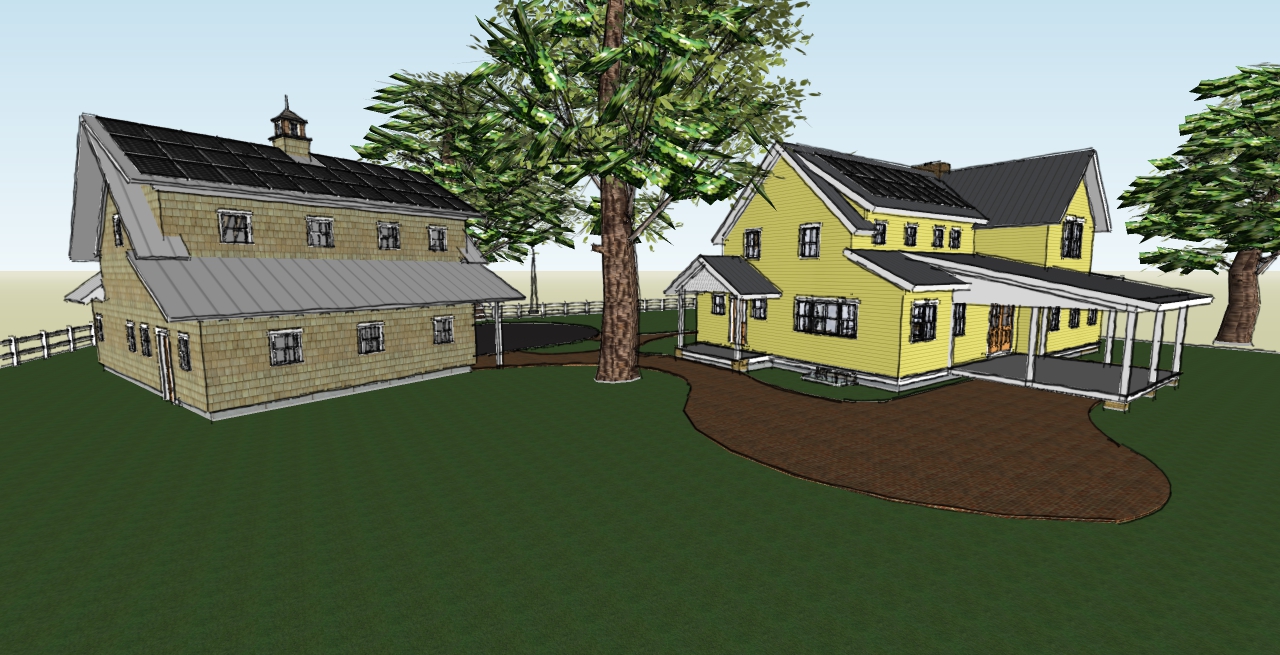
Number of Bathrooms:
Scope Description:
Non-residential uses will include workshop type activities in barn/garage, and a great portion of the finished basement in the house.
Site conditions:
Renewable Energy Sources:
Other Purchased Fuels Description:
No
Summary of enclosure strategy/description:
PERSIST/REMOTE technique. Liquid applied barriers when possible to prevent peel-back and other issues with pressure applied air barriers. Super Insulation, multi-layer, offset seams throughout project.
Roof Assembly:
standing seam, 5/8" plywood, cold roof vent, supplemental rafter/cold roof, 6 layers of 2.75 EPS, Vapor barrier, 1/2" OSB, barnboard strip sheathing (exposed to interior), exposed rafters.
Roof R-value:
Window Description:
Marvin Next Generation Triple Pane
Door Description:
Therma Tru
Mechanical Equipment Installation Details and Comments:
blower door to be done.