Project Description:
Our home is a 120-year-old farmhouse in downtown Amherst, MA. At the time of purchase, it had no insulation in the walls or attic, was heated by an oil furnace from the early 20th century, and was clad in mint-green asbestos shingles. Although walking distance to downtown, all of the public schools, and in a wonderful neighborhood, it gave us pause. On the plus side, the foundation was a quarter inch off of square, the framing was sound and the orientation produced a long south face. We seriously considered knocking it down but philosophically decided that we had stumbled on a perfect candidate for a deep energy retrofit. In short, we decided to keep as much of the structure of possible while attempting to address our needs now and into the future.
At no point was our goal to create a net zero house;Rather, we sought to make the best once-in-a-lifetime decisions. This approach led us to focus on creating a highly efficient building envelope. Our guiding principles for the functional design were few: (1) insist that every square foot be usable space (2) accommodate our young family with two children and a cat (3) establish spaces to accommodate the reality of our lives (mud room for kids boots, guest room for family and friends, and office for parents who work late), (4) allocate capital to core projects and leave long-term desires for a later date (garage and screened-in porch).
The result of our efforts is a highly efficient home with uncompromising aesthetics and comfort. The original footprint of the house is unchanged and yet we were able to massively upgrade the functional and energy efficiency of the site through smart design. For example, by removing and redesigning the roof, we were able to achieve three things: increase headroom in order to create a third-floor guest suite and office, remove a gable interrupting the south roof face to maximize space for PV, and create deep rafter bays for increased insulation. By clustering the auxiliary spaces in our home (office and guest suite) on the third floor and through our multi-zone heat pump system, we are able to “power down” those areas when not in use.
We have been in the house for a year and a half. It is a joy to live in. First, we relish living in a house designed to our needs and aesthetics. Our floor plan places living spaces on the south side and puts transition spaces on the north side so our primary living spaces and every bedroom is sun-splashed. Second, we are extremely proud to be a net clean energy producer. Despite running only electric appliances (including a lawn mower) we generate 30% more energy than we consume. We achieved these great heights by using a limited set of well-proven and accessible technologies and design elements. Our house is living proof that the existing housing stock of this country can be transformed to provide beauty, comfort, and sustainability.
Building Type Summary:
Address:
Elevation:
Lat. / Long.:
Location Type:
Köppen Climate Type:
Climate Region:
Solar Insolation:
Annual HDD :
Annual CDD:
HDD Base Temp:
CDD Base Temp:
Occupancy Type and Details:
During the 12 month period for which data is collected, the building was occupied for 360 days of the year. This is our full time residence, and we were away for only one vacation during the observation period.
In addition, the house supported 1,710 person days. In addition to our family of 4, we also housed my sister’s family of 3 for a 3-month period (April – June 2011).
Conditioned Floor Area:
Unconditioned Floor Area:
Multiple buildings?:
Total number of units in project (all buildings):
Total floor area of project (all buildings):
Historic?:
Completion date:
Annual renewable energy generated:
Electric Utility Company:
Datasets and Utility Bills sources and reliability:
data sourced from utility bills
Electricity amount (imported from grid):
Electricity amount (credited or exported to grid):
Net electricity usage (purchased electricity):
Subslab assembly:
Existing slab was retained; no sub-slab insulation installed.
Slab edge assembly:
Existing slab was retained; no slab-edge insulation added.
Foundation wall assembly:
Brick and Fieldstone foundation wall insulated to the inside with closed cell spray foam to R-30 (5 inches)
Above grade wall assembly:
R-33+. Existing Above Grade Walls - 4” studs with existing board sheathing – retained. New Walls with 2x6 framing.
All walls insulated to the outside with (2) 1.5” layers of foil-faced polyiso, staggered and taped at all seams as air barrier.
Walls insulated to the inside with 4” (or 5.5”) Open Cell Spray Foam. Here, the use of open cell foam avoids a double vapor barrier at the above grade framing and sheathing, and provides further air barrier adhered to the existing board sheathing.
Flat attic assembly:
Small portions of the third floor have flat ceilings, with lighting and refrigerant piping concealed above.
Cathedral ceiling assembly:
Entire roof re-framed with 2x12 rafters to provide deep cavity for cellulose. Insulated to the outside with the same 3” of polyiso for an R-54 roof assembly.
Space heating - Manufacturer & Model:
Space cooling - Manufacturer & Model:
Domestic hot water - Manufacturer & Model:
Domestic hot water - capacity:
Ventilation - Manufacturer & Model:
Finances Description:
Our construction costs totaled $708,782. Excluding the design costs of $48,256 and site preparation and landscaping costs of ($32,500), leads to an adjusted project cost of $628,026. This includes costs for insulating our basement and construction management services.
Total Cost of Project:
NESEA Awards:
NESEA Zero Net Energy Building Award 2012 Winner
Energy Use and Production Documentation:
Foundation wall R-value:
Above grade wall R-value:
Average window U-factor:
Project Photos:

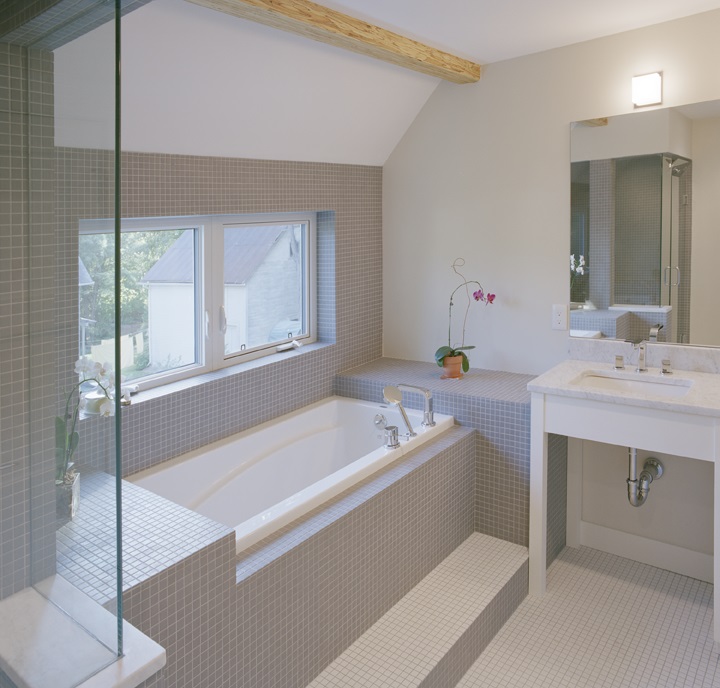


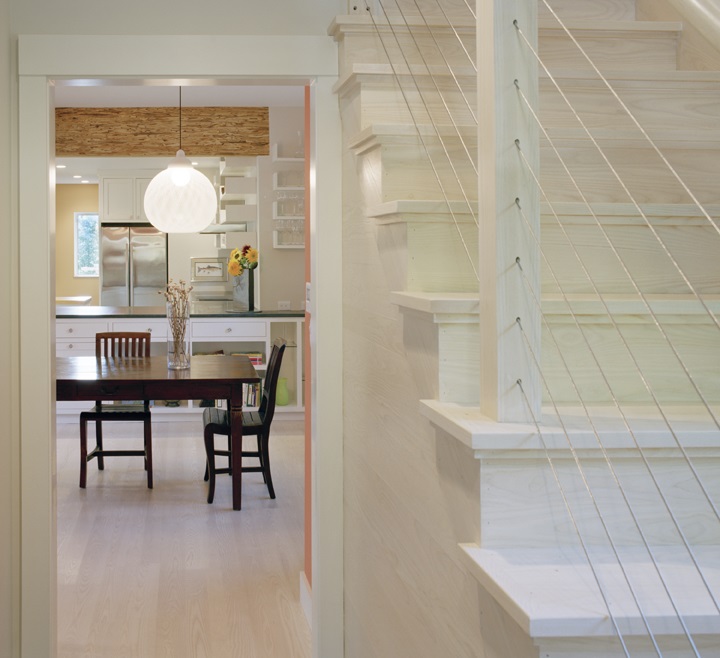
Number of Bathrooms:
Site conditions:
Renewable Energy Sources:
Window Description:
49 windows from Fibertec, Casement 300 series. U-values range from 0.13 – 0.18 for fixed, awning, and casements.
Door Description:
2 doors from Fibertec, 200 series, Triple-pane, low-e. 1 door from Simpson (Model 7008 w/ insulated glass)
Mechanical Equipment Installation Details and Comments:
Lighting in the house is predominantly achieved through 46 Juno LED cans. In bedrooms and in bathrooms, ceiling mounts and sconces use CFLs and halogens. Total lighting is 0.88W/sf.