Project Subtitle:
Project Description:
This new house at Katywil Community,in Colrain Massachusrtts, was occupied in September 2015. This house is slightly larger than the other houses built here recently at almost 2200 SF, but it has passed the Passive House standard of Air tightness at .45 ACH50.
This is a house for a couple with a young daughterand a small herd of goats. It is located on a south sloping abandoned orcherd. The entry to the main level is on the north side. The main level includes a mud room, kitchen, living/ dining area and a flexible space with a toilet off of it. The flex space can become a bedroom and the bathroom has a barrier free shower. The main living area includes a cathedral ceiling. The lower level includes two bedrooms, a bathroom, utility room and an unheated root cellar. The main level also has a screened in Porch, a small deck on the south side and a single car garage on the north.
This is an all electric house but it also has a Tulikivi masonry wood fired heater which is planned to provide a major portion of the heat. The lower level includes an air source mini-split heat pump sized to heat the whole house if necesary. Domestic hot water is provided by a heat pump water heater. They plan to install an 8 kW PV solar array in the future.
Building Type Summary:
Address:
Elevation:
Lat. / Long.:
Location Type:
Climate Region:
HDD Base Temp:
CDD Base Temp:
Occupancy Type and Details:
Owner occupied. The house is generally occupied by someone full-time by a couple and one child. They work from home most days except when on vacation.
Conditioned Floor Area:
Conditioned Building Volume:
Semiconditioned Floor Area:
Unconditioned Floor Area:
Multiple buildings?:
Total number of units in project (all buildings):
Total floor area of project (all buildings):
Historic?:
Completion date:
Site description:
The site is a southern sloping abandoned orchard,
Materials:
This house is constructed with long-lasting materials to create a tight passive solar house to be heated with renewable sources and no onsite fossil fuel use.
It is a wood frame house on a poured concrete foundation, using Zip sheathing as the air/water barrier and clad with Hardie plank composite siding. The roofing is long lasting Fabral metal roofing.
Energy Highlights:
This is a passive solar design, that is highly insulated to keep the heat in the house. It is wired for the addition of an 8 kW solar array in the future.
The house has a very low heat load so it can be with a single mini-split heat pump. Heating of the main level is met with a wood fired masonry heater that holds the heat of the fire for a long time and re-radiates it back to the living space.
LCA Description:
The whole house was built with high quality low maintenance materials.
Subslab assembly:
The lower level floor slab includes water tubing for a possible future air/water heat pump system. The slab is insulated by 4" of polyurethane (R 20)under the slab and 2" around the edge of slab (R 10) and interior of the foundation.
Slab edge assembly:
2" polyurethane running up the interior of the foundation, separating it from the slab as a thermal break from the slab which could be heated.
Foundation wall assembly:
Where the heated area is below grade the insulation includes 2" of polyurethane against the foundation. That is covered by a 2 x 4 stud wall which was netted and blown with 4" cellulose dense packed insulation and covered with gypsum board. The band joist an floor joists were sealed with urethane spray foam insulation at least 8" deep.
Above grade wall assembly:
The above grade walls are insulated with 12" of dense packed cellulose. The walls are double studded to reduce thermal bridging.
Flat attic assembly:
The attic and roof is composed of roof trusses. The roof is vented at eaves and ridge. The ceiling flats are insulated with loose blown cellulose.
The ceiling is composed of taped Zip wall sheathing air barrier covered by gypsum board.
Cathedral ceiling assembly:
NA
Door Area:
Space heating - Manufacturer & Model:
Domestic hot water - Manufacturer & Model:
Domestic hot water - capacity:
Domestic hot water - efficiency:
Ventilation - Manufacturer & Model:
Special architectural measures:
This house is a passive solar design with many large southern windows equal to 8% of the floor area, and it faces directly south. They are shaded by wide overhanging eaves. the above grade walls are 12" deep double stud design for an R 42 rating. The Southern facing glass in the windows was specified with a higher heat gain than the other windows.
Energy Strategies:
The strategy is to reduce the heat load by making the most of the solar gain, reduce the heat loss by building a very tight, very well insulated house so the heating can be managed by burning wood and a mini-split heat pump. The energy needed then can be handled by a PV solar array. The owners plan to purchase very efficient appliances and cook with an induction stove and bake bread with the wood masonry heater. The hot water is made by an efficient heat pump water heater.
Subslab R-value:
Slab edge R-value:
Foundation wall R-value:
Above grade wall R-value:
Flat attic R-value:
Cathedral ceiling R-value:
Average window U-factor:
Solar Heat Gain Coefficient:
Door U-Factor:
Air Changes per hour, ACH50:
Project Photos:
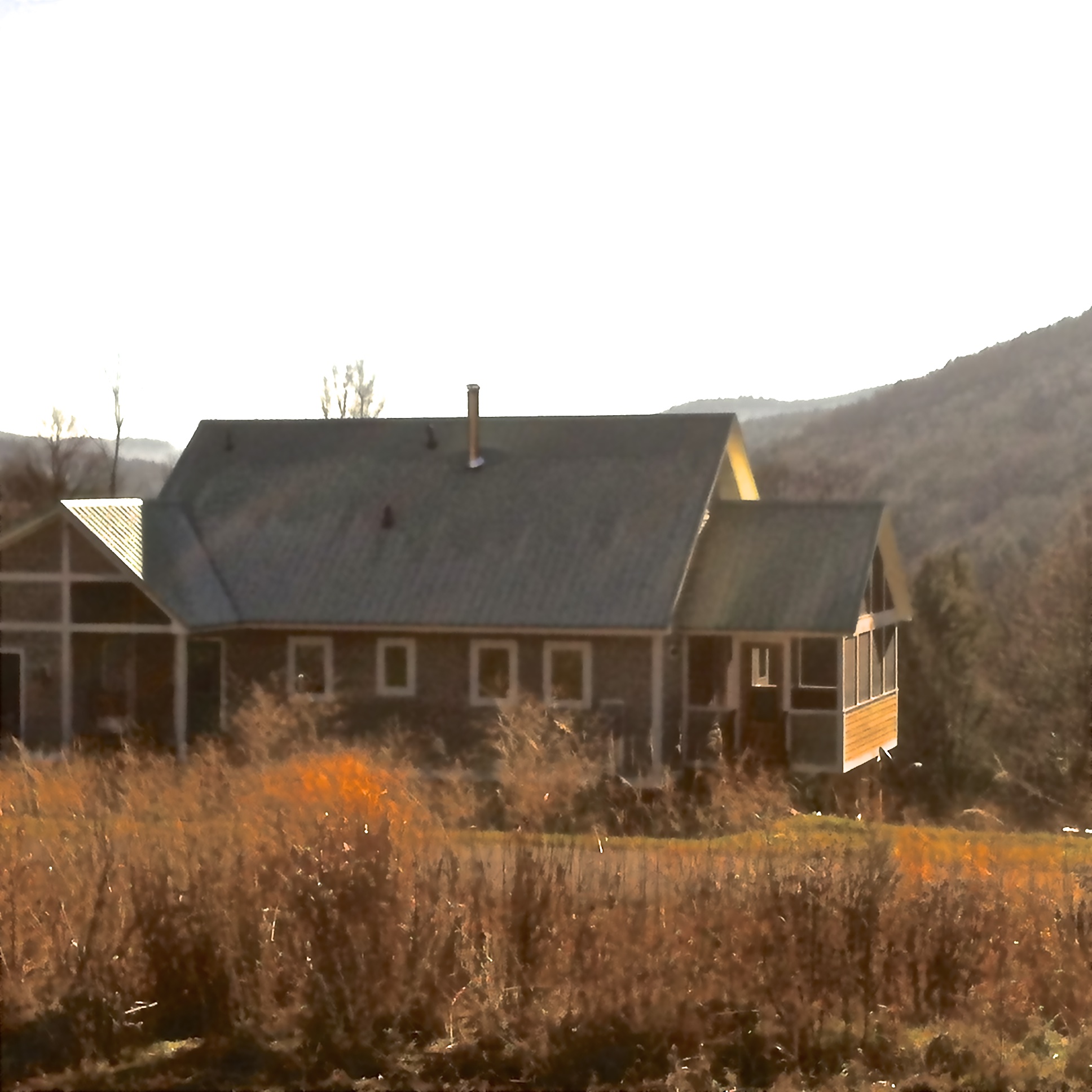
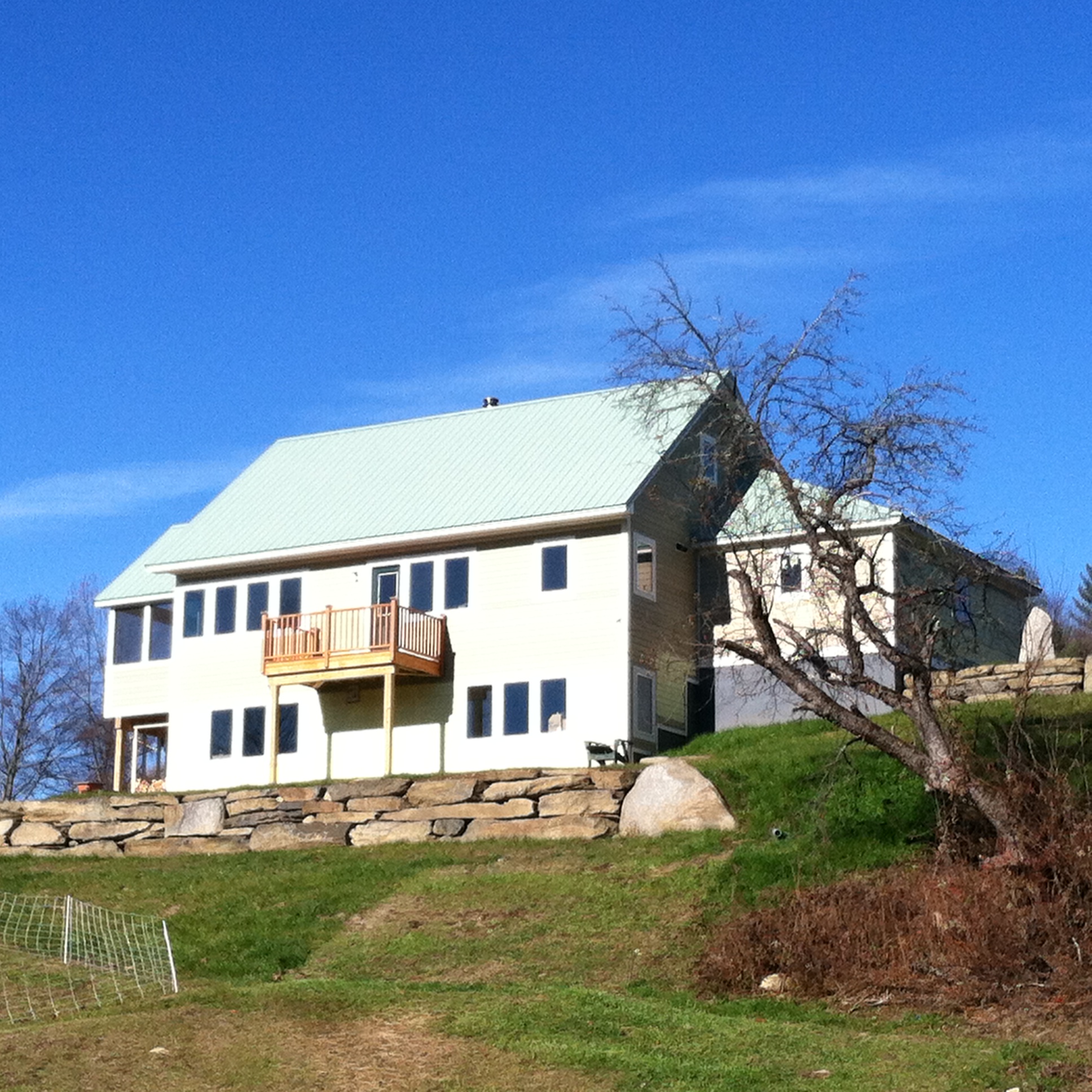
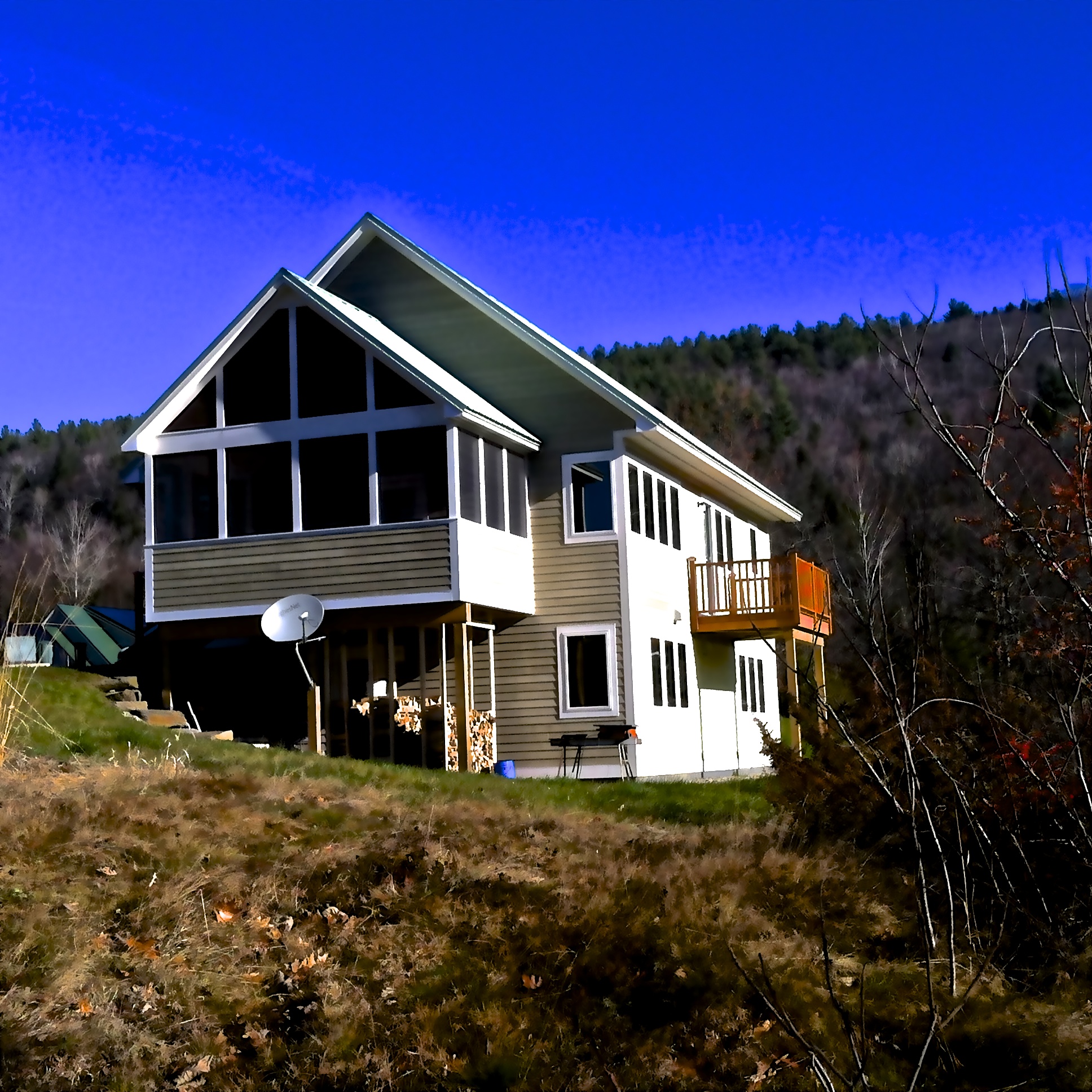
Number of Bathrooms:
Scope Description:
This house is new construction including excavation, utilities, sewage and landscape.
Site conditions:
Summary of enclosure strategy/description:
The building envelope passes the Passiv Haus standard < .5 ACH50. It will be a supper insulated envelope with an efficient Heat Recovery Ventilator.
The wood stove has an insulated outdoor air supply.
Roof Assembly:
The roof is 5/8" plywood sheathing covered with ware proof underlayment and Fabral metal roofing.
Roof R-value:
Window Description:
Windows are double glazed Wethersheild fiberglass windows. South facing windows are low-e argon filled with a heat gain coefficient of 3.0.
North facing windows are glazed with Zo-E Sheild 8 glazing which is low E but a lower heat gain and lower light transmission.
Door Description:
All doors are Therma-tru smooth star fiberglass doors.