Project Subtitle:
Project Description:
"Minus eighteen degrees outside, sixty-eight degrees inside, and zero ice dams!"
House Owner
This 2,400 SF four-bedroom house was designed for a growing family with a very tight budget. Construction was largely completed by the end of July of 2014.
The project is located on a 15-acre northwest sloping site in Vermont’s Northeast Kingdom. Willoughby Gap dominates the panoramic southwest-to-northwest view, and the owners wanted to see this dramatic feature from main living areas. For this reason, and because of the grades, the narrow end of the house faces northwest, and the long axis of the house follows the fall line of the hill. Locating the house high on the hill improves the views and leaves the majority of the land available for growing hay.
Meeting the budget constraints required a simple building form with a straightforward structural system. The narrow plan eliminates interior columns. Except for the minimal disruption of the stair, joists and roof trusses span the width and march down the length of the house. The simple, economical gable form is a reinterpretation of local vernacular buildings.
The house has three bedrooms and two bathrooms on the second floor, with the master suite separated from the smaller bedrooms by the stair. The small size of the children’s bedrooms is offset by the wider common play/study hall (with a view of the valley at the end). On the main level, kitchen, dining, and living are combined; beyond the stair is air study/bedroom with a possible en- suite configuration. A studio and a play/exercise area occupy the 400 SF above-grade end of the basement.
Two air-source heat pumps, one in the basement and one on the main level, heat the house. A small wood stove provides backup heat. Floor grates, salvaged from a renovation project, allow heat to move up to the second floor. All the bedrooms have provision for installing radiant ceiling panels for supplemental heat, but the owners do not think that will be necessary. An HRV provides balanced ventilation. A heat pump water heater supplies domestic hot water.
The owners are completing designed interior and exterior features of the house as time and budget allow. Salvaged stone steps and steel steps at the front and back doors respectively provide access to the main level from outside. A custom wood railing protects the second floor opening above the front door.
Building Type Summary:
Other Awards:
None.
Address:
Elevation:
Lat. / Long.:
Location Type:
Köppen Climate Type:
Climate Region:
Solar Insolation:
Annual HDD :
Annual CDD:
HDD Base Temp:
CDD Base Temp:
Occupancy Type and Details:
Owner-occupied; two adults and one child.
Conditioned Floor Area:
Conditioned Building Volume:
Semiconditioned Floor Area:
Unconditioned Floor Area:
Multiple buildings?:
Total number of units in project (all buildings):
Total floor area of project (all buildings):
Historic?:
Completion date:
Site description:
15+- acre sloping site. The uphill (southeast) boundary is wooded. The downhill (southwest) and the northwest sides of the property are bounded by roads. The site is mostly open meadow. It has a panoramic view from the southwest to the northwest.
Materials:
The house is small and simple, and that means construction was somewhat more efficient. An attempt was made to balance cut and fill in the design of the site.
Energy Highlights:
Air-source heat pumps in a very cold climate zone
LCA Description:
No
Annual renewable energy generated:
Electric Utility Company:
Datasets and Utility Bills sources and reliability:
Village of Lyndonville, VT Electric Department
Internet tracking of the solar array
Electricity amount (imported from grid):
Electricity amount (credited or exported to grid):
Net electricity usage (purchased electricity):
Energy Storage type:
Not applicable
Subslab assembly:
Rigid foam
Slab edge assembly:
Rigid foam separating the concrete floor slab from the concrete walls
Foundation wall assembly:
Concrete walls
Above grade wall assembly:
2x6 studs filled with blown cellulose; Zipp system sheathing taped; two 2" layers of foam, joints offset and taped; vertical strips; siding.
Cathedral ceiling assembly:
Scissors trusses blown full of cellulose; Zipp roof sheathing with joints taped; two 2" layers of foam, joints offset and taped; nailing surface; metal roofing.
Door Area:
Space heating - Manufacturer & Model:
Space heating - capacity:
Space cooling - Manufacturer & Model:
Space cooling - capacity:
Domestic hot water - Manufacturer & Model:
Domestic hot water - capacity:
Domestic hot water - efficiency:
Ventilation - Manufacturer & Model:
Process:
This house was designed in conduction with Marc Rosenbaum's NESEA Masters course on Net Zero Homes. After visiting and documenting the site, the architect and owners developed a detailed list of wishes and needs. Design was an iterative process, with multiple drawings submitted to the owners for review. Based on the best scheme, one of the owners built a model for final review. The construction manager joined the team during the design process to provide estimates.
Design for Adaptability:
The study/guest room on the first floor level is large enough serve as a full bedroom should someone find it difficult to negotiate stairs. There is an adjacent closet and bathroom that, with the closing of a sliding door, can become a bedroom suite.
Other Software tools:
PowerCadd was the drafting program. SketchUp was used to create preliminary renderings.
Energy Modeling Software:
Energy use was modeled using the spreadsheets provided in Marc Rosenbaum's Zero Energy Homes Masters course.
Outcome of project goals:
Simplifying the overall design of the house made it possible to meet the owners' budget goal. Based on comments from the owners and my own repeated visits to the house, orienting the house along the slope and toward the view (long axis northwest/southeast instead of
Discrepancies:
So far, the project has fallen short of the net zero energy goal. One reason for this may be due to the first/second floor heat pump. The eMonitor showed that it was short-cycling (something not possible to determine from the utility invoices). A review of the literature yielded the recommendation that we install a remote thermostat; this was specified but not installed by the builder. During the installation we found that the line sets for both heat pumps had not been properly sealed where they penetrate the exterior wall. As a result, dead mice and wasp nests were found in the heat pump. We also discovered a refrigerant leak. And the unit had never been cleaned at the end of construction. Our hope is that this unit, a key element in the heating system, will perform significantly better this coming winter. Already, the owners have noticed an improvement.
We will continue to monitor and refine performance.
Finances Description:
The project was financed with a mortgage and downpayment. Overall costs have been withheld at the owners' request.
Gross Cost of Renewable Energy System:
Value of Tax Credits for renewable energy systems:
Net Cost of renewable energy systems:
Federal incentives:
$8,400
State incentives:
$1,500
Other incentives:
None
NESEA Awards:
None.
Published References:
None.
Special architectural measures:
The envelope is super-insulated. The long dimension of the house runs southeast/northwest, with the long side of the house roughly 15-20 degrees west of true south, so there is a significant amount of solar gain. The opposite side of the house has a reduced number of windows.
Energy Strategies:
The envelope is super-insulated. House orientation and window arrangement favor solar gain in cold months.
Energy Use and Production Documentation:
Subslab R-value:
Slab edge R-value:
Foundation wall R-value:
Above grade wall R-value:
Cathedral ceiling R-value:
Average window U-factor:
Solar Heat Gain Coefficient:
Visible Light Transmittance:
Door U-Factor:
Air Changes per hour, ACH50:
Project Photos:
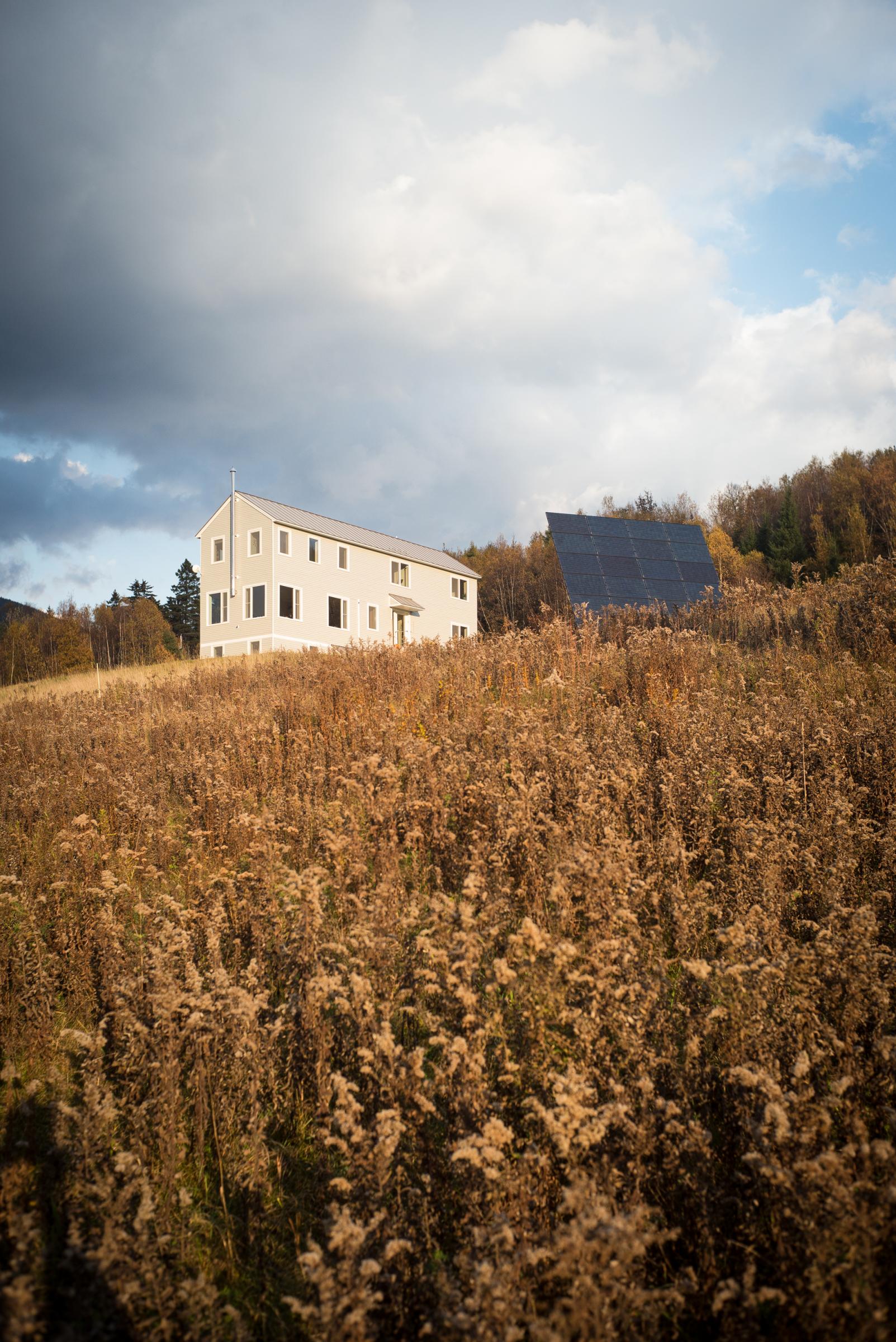
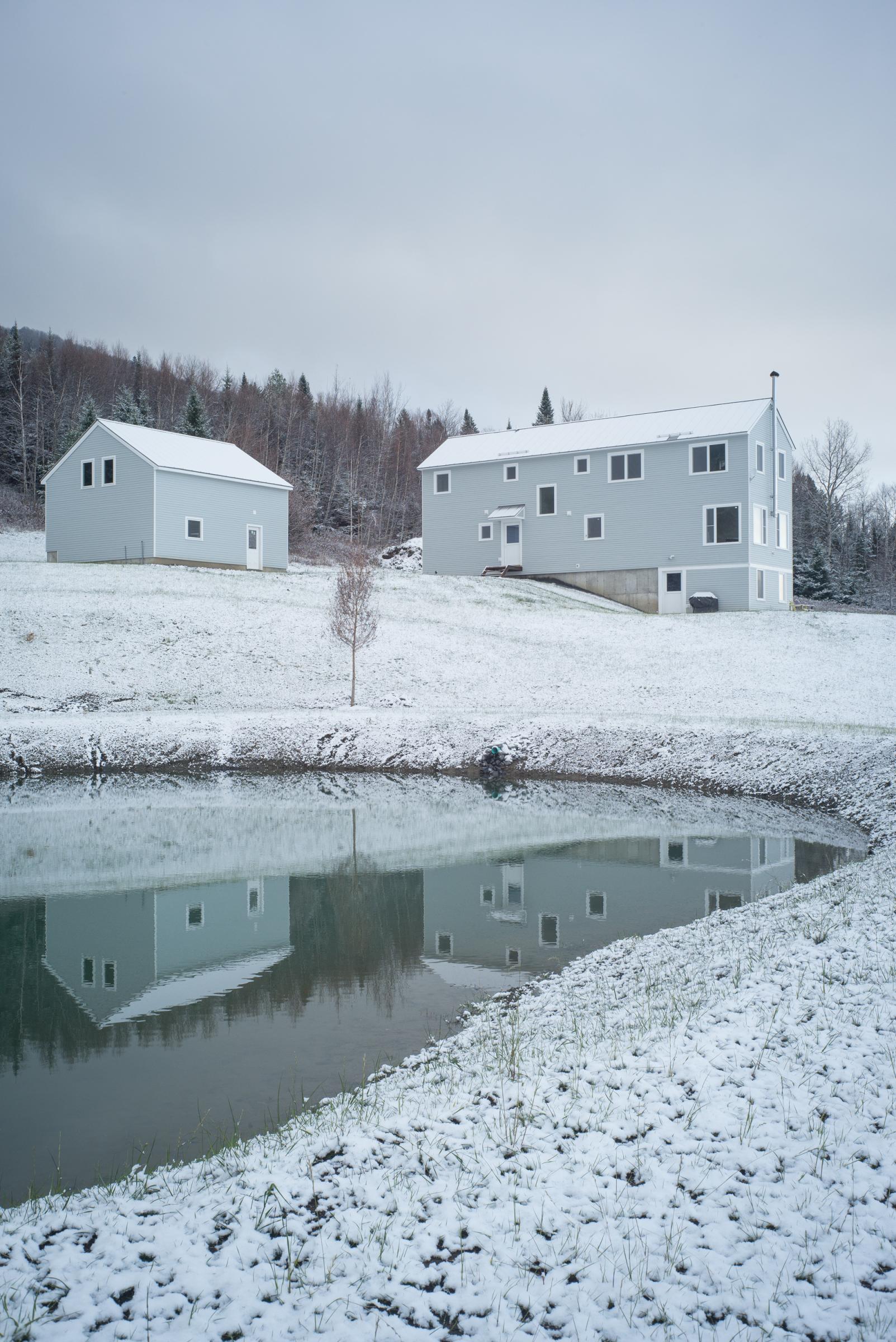
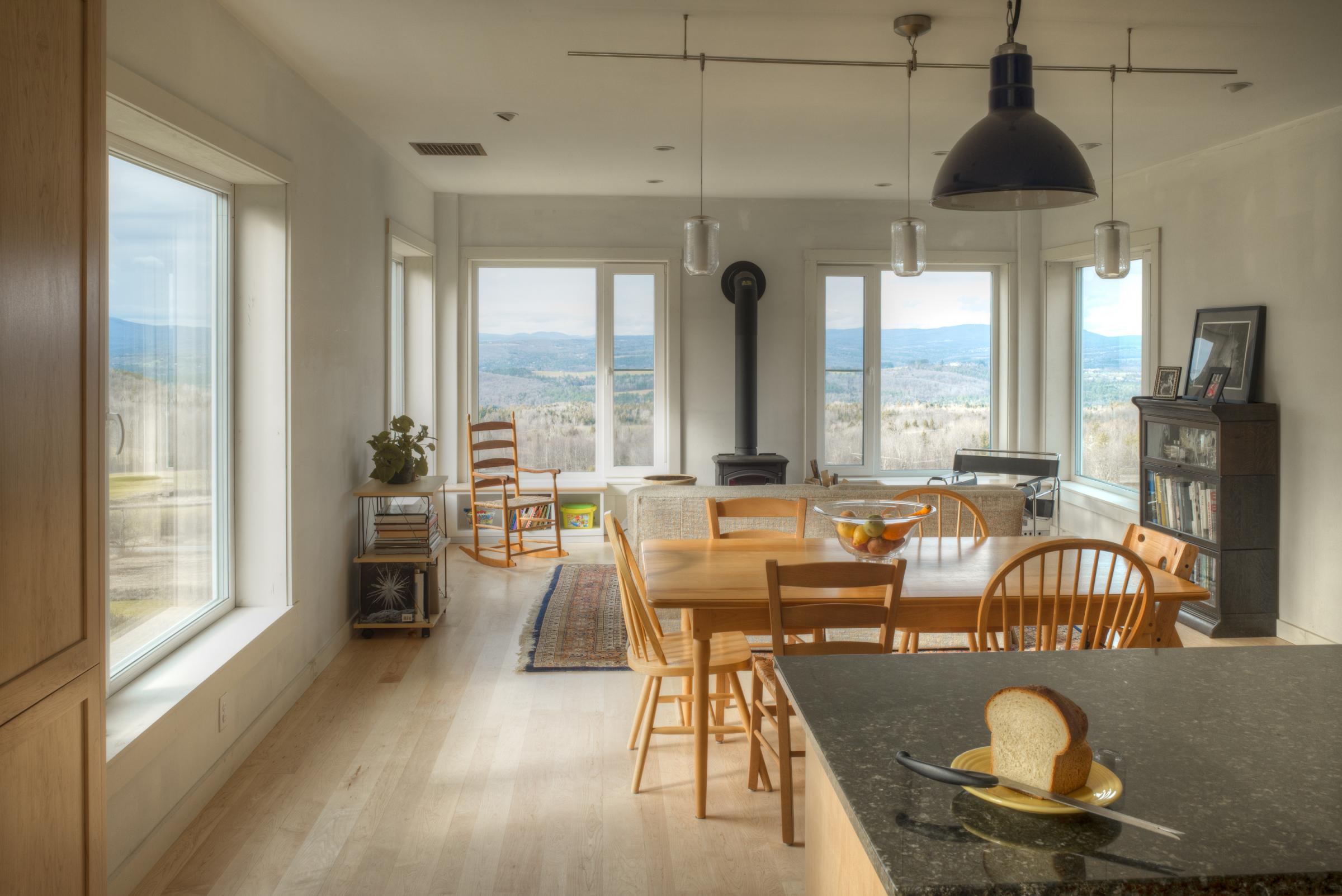
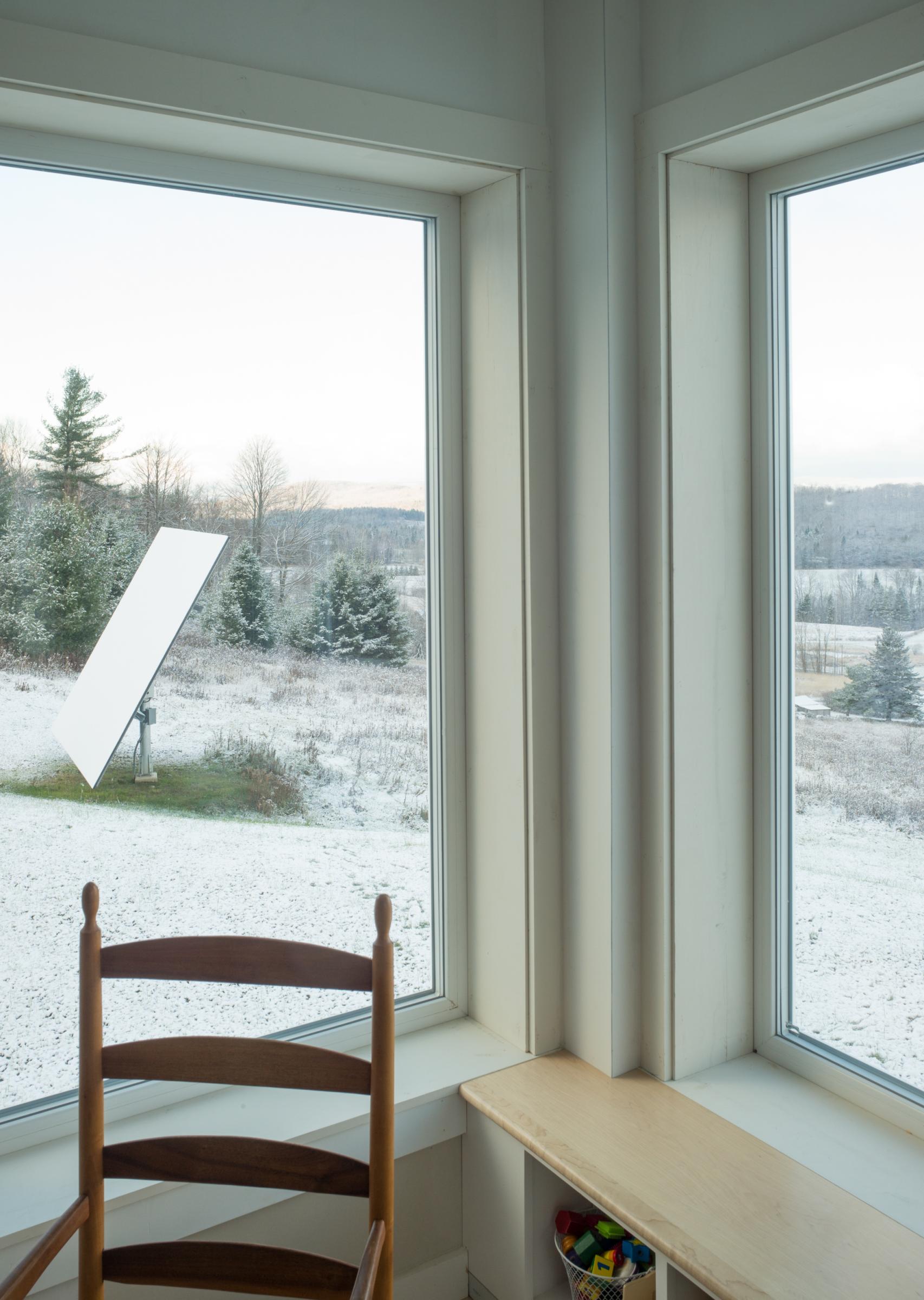
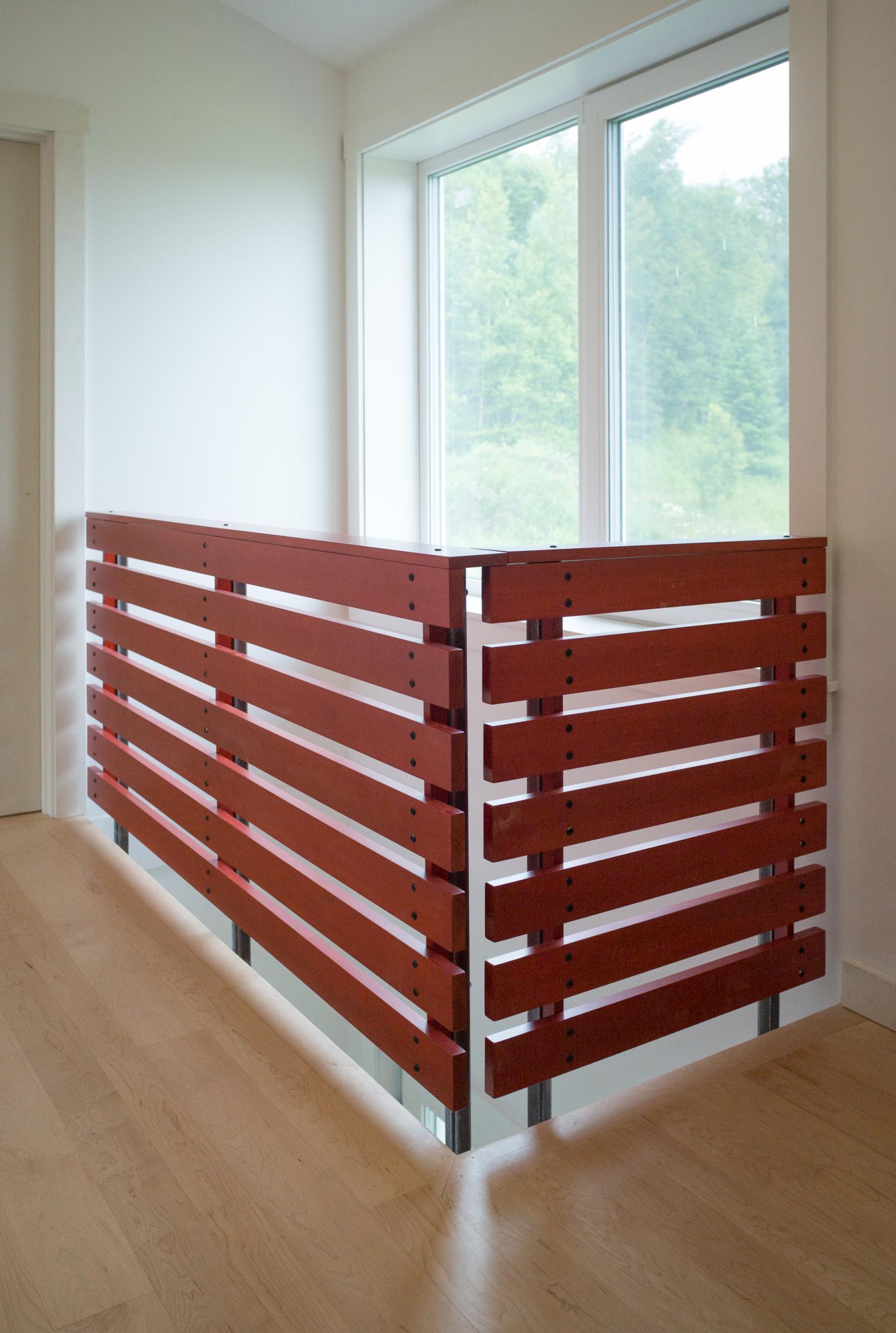
Number of Bathrooms:
Scope Description:
New house with detached unheated garage.
Site conditions:
Renewable Energy Sources:
Other Purchased Fuels Description:
One cord of wood
Summary of enclosure strategy/description:
Super-insulated envelope. Air tightness tested by fog machine and blower door.
Roof Assembly:
See above.
Roof R-value:
Window Description:
Intus PVC windows and doors, triple-glazed
Door Description:
Intus PVC windows and doors, triple-glazed
Number of Bedrooms:
Project Team:
Team Member:
Team Members:
Tirey & Associates, Structural Engineers
Fritz Fay, Construction Manager
Mechanical Equipment Installation Details and Comments:
Blower door test and tracking with eMonitor