Project Subtitle:
Project Description:
This project takes the long-term investment of a high energy performance home (Zero Net Energy) and adds function and value by adding a multi-generational use layout and incorporating aging-in-place features. Although privately funded, the project was used to demonstrate (via www.rcmzeroenergy.com) what could be accomplished in undertaking a ZNE residential construction (2011-2012) and to share the knowledge and explain reasons behind the approach. The purpose of the website was to educate owners, designers, builders, and developers to the how’s and why’s of undertaking high performance residential construction that starts with high performance enclosure design and ends with renewable energy technologies.
One story living is accomplished on the upper at-grade level. Given the extraordinary expense of assisted care and/or nursing home living, a modest investment in making a new home suitable for people to grow old in adds significant value to the home. A stacked washer-dryer laundry area across from the first floor powder room is sufficient to serve an older couple if/when the larger, lower level laundry room is no longer an option due to physical limitations. The garage has an extended depth and houses a dry storage room, as well as a 4’ wide ramp up the three steps to the entry area. The garage width is also enlarged for easier car egress mobility. Groceries can be “wheeled” in using a simple 2-wheel, lightweight, aluminum cart. The outdoor spa is included in the Net Zero design and is sunken into the deck with an inclined grab bar to facilitate an older person’s easy entry, and is roofed over to facilitate year round, all-weather use.
All of the passage doors on both levels are 36" wide (34" for pocket doors). The large NanaWall folding/sliding door to the 3-season room has an ADA threshold, and there is no step down from the interior space to the 3-season room. Space has been allocated in the home for wheelchair mobility and access. Simple ramps can be easily added later (if required) to transition the 8" differential height from the home’s interior to the outside rear deck. Pre-wiring and blocking has been included to allow for automatic door operator systems to be installed later (if required) on the entry door from the garage which already incorporates an ADA threshold.
Since we were focusing on an aging-in-place design, the lower level is readily convertible into a one level, two bedroom, in-law suite or caregiver suite by using the whole lower level finished space as a “two family” type, two bedroom design. It can also transform into a one bedroom caregiver suite by adding one simple straight partition wall to divide up the “gathering” space area; thereby splitting up the lower level space for dual use between upper and lower inhabitants. The gathering space already has a fully functioning kitchen along one wall. Direct access and parking for the lower level is also provided at the rear of the home. Alternatively, the same space could be used immediately for a younger extended family. There is ample outdoor living space at each level.
This project occupies a piece of land that was previously used as the “boneyard” of historic farmlands that were vibrant over the past two hundred years. The open space green “pasture” land to the south is now preserved as an agricultural conservation area by this project. The actual project structures sit on what once was the rocky, sloping woodland to the north. Crumbling stone walls have been rebuilt and the abundant wildlife is still able to feed and move about the property as they did before. Wild turkeys, hawks, owls, ducks, geese, herons, kingfishers, deer, bobcats, fox, bear and the occasional migrating bald eagle have all been observed. The public parking and boat launch facility across the pond is regularly used by fisherman and kayakers throughout three seasons, and by ice fisherman and skaters during the winter.
Building Type Summary:
Other Awards:
BOSCH GREEN LIVING AWARD 2013
MARVIN ARCHITECT'S CHALLENGE SHOWDOWN PEOPLES CHOICE AWARD WINNER 2013
CORNERSTONE AWARDS (3) by the Home Builders and Remodelers Association of New Hampshire (HBRANH) 2014
USPTO AWARDED 2014 (US Patent No. 8,733,429 ) SOLAR-GEOTHERMAL HYBRID DESIGN
Address:
Elevation:
Lat. / Long.:
Location Type:
Köppen Climate Type:
Climate Region:
Solar Insolation:
Annual HDD :
Annual CDD:
HDD Base Temp:
CDD Base Temp:
Occupancy Type and Details:
Owner occupied.
2.5 ave occupants.
24 hour occupancy.
Conditioned Floor Area:
Conditioned Building Volume:
Semiconditioned Floor Area:
Multiple buildings?:
Total number of units in project (all buildings):
Total floor area of project (all buildings):
Historic?:
Completion date:
Site description:
Situated on a formerly overgrown section of farmland and scrub woodlands, the site offered no naturally flat or attractive terrain within the buildable area limits of the 8.86 acre lot. The best buildable land on the lot was preserved as open farmland through a conservation easement. The vast majority of the trees cut for project development were not commercially viable and were converted on site into woodchips that were used for erosion control berms and ground cover stabilization. All of the topsoil removed for project development was stockpiled, sifted, and then converted into loam for use on the project, and the surplus loam was exchanged by the site contractor for other gravel materials required for driveway construction. All large stone removed during the project excavations were extensively re-used later as free standing stone wall construction, vertical stone retaining wall construction, and inclined slope “armoring”. All small stone, stumps, and farm debris were buried on site as common fill.
The finished site design extends the green pasture lands to the east, down to the new access drive, and new grasses flow into the upper terrain of the vegetable and perennial gardens. These areas were previously scrub woodlands, tangled and overgrown bushes and vines, and farm debris. The newly created tiers of the project layout and design extend over four distinct levels: the upper natural grade fields and gardens; the driveway, first floor residence, and garages (2) at-grade access; the lower level floor at-grade access and septic field/lawn; and the lowest level natural grade of woodlands and grasses. The two at-grade levels of the house design embrace the naturally sloping terrain and are integral to both the economics of “earth berm” construction and zero net energy performance.
Large prominent trees consisting of maple, white oak, red oak, eastern pine, shag bark hickory, and pignut hickory have been painstakingly preserved within the project’s buildable area. All species of trees and shrubs are preserved within the conservation area. Some of the existing species of softwood trees and natural grasses were also transplanted within the newly landscaped areas of the project. Native species were also purchased from New Hampshire nurseries. A small orchard of mixed semi-dwarf varieties was planted on gently sloping terrain that would otherwise be unused, as it connects the upper main access drive, the side drive that provides access to the lower level in the rear, and the lower level lawn/leaching field. All new lawn areas and grass field extensions were seeded and grown in-place.
A comprehensive stormwater runoff collection and redistribution design was implemented to make sure that pocket wetland areas below the site would be properly recharged. A compliment to that strategy was to divert some of the upper level roof runoff directly into a perimeter drain system of the house that must first saturate a 2,500 sf +/- area of a 12” deep sand bend layer that houses some 7,500 lf of “slinky” solar-geothermal hybrid ground loop lines, before exiting the perimeter drain system.
The home is accessed via a 700'+ long x 18' wide gravel drive. The width was increased to 18' to accommodate two-way traffic. At the terminus of the gravel driveway (carriage garage location) it transitions into concrete panels that connect the driveway, house entry, attached garage, and detached garage via an approximate 70' diameter “courtyard”. Drainage from the concrete pitches to a catch basin located on the western edge. There is ample room for snow removal and snow storage along the easterly side of the courtyard.
The full perimeter of the home is accessible via a (minimum) 12' wide gravel access drive with a maximum 10 degree slope, which is suitable for winter travel by front wheel drive or all-wheel drive vehicles. The adjacent pond is accessed by a 6' wide gravel trail suitable for walking and also accessible by an ATV or garden tractor. There is a 10'x10' wooden platform at the shore of the pond with a dock connected to it in the summer. The pond is accessible for recreational use all 12 months of the year.
Materials:
Materials were selected based on a number of criteria, but in general reflect the long life cycle nature of the home’s design, due to the multiple themes of zero net energy performance, aging-in-place life planning, and multi-generational living, all of which have a potential long ownership plan associated with it. Durability and low maintenance held a particularly strong place in that field, but they also play into the themes of our sustainable, recycled and/or recyclable, and green criteria as well. For example, long life CertainTeed products were used for roofing, siding, trim board, decking, railing and soffit applications. We also took advantage of locally sourced products wherever possible, but never to the detriment of life cycle. For instance, all the ground covers (bark mulch or wood chips) were either created on site with site materials or made 25 minutes away from wood waste products. Also, our large architectural timber frames, timber trusses, and wood beams were fabricated by Thurston Millworks, a millwork shop just ¼ mile away, from domestic, sustainable forest timbers.
Interior/exterior materials include US made, high recycled content porcelain tile flooring by Stonepeak Ceramics for long life and low maintenance; painted concrete flooring, integral colored concrete flooring; Greenguard certified cabinetry by Executive Cabinetry; a small zero carbon footprint manufactured outdoor spa tub by Hydropools; and zero VOC paint finishes by Glidden Professional. US made interior hardwood doors, stair parts, hardwood flooring, hardwood work benches, and office work benches all came from Baird Brothers Fine Hardwoods, a company that heats and cures with its own wood wastes and generates its own electricity from a methane gas field.
On the site wood waste, cardboard, and loose metals were not permitted in the dumpster. All wood was cut for use as space heating or recycled into site (bark mulch/wood chips) landscaping products. All cardboard and metals were hauled to local recycling centers.
Energy Highlights:
The project combines the use of PV panels with a back-up battery bank; solar thermal panels; geothermal heat pumps (2); a hybrid design that integrates excess BTU production from the solar thermal system to boost the effective COP of the geothermal system with both space heating BTU's via the buffer tank as well as a wet sand heat sink below the building; a dedicated air-air HRV for fresh air; and an on-demand electric back-up domestic hot water heater. The HERS rating of the home, before inclusion of the PV system, was calculated to be 35. The project has performed each calendar year (3 total) at zero net for each year of the 3 years, including the use of the outdoor spa which is metered internally for record purposes, and consumes approximately 10% of the PV output.
The Geo-Solar Hybrid system sees an annual ground temperature (recorded) swing from approximately 40 deg F late winter to 75 deg F late summer. The peak COP for the hybrid performance is estimated to reach a max of 5.0.
LCA Description:
Materials were selected based on a number of criteria, but in general reflect the long life cycle nature of the home’s design, due to the multiple themes of zero net energy performance, aging-in-place life planning, and multi-generational living, all of which have a potential long ownership plan associated with it. Durability and low maintenance held a particularly strong place in that field, but they also play into the themes of our sustainable, recycled and/or recyclable, and green criteria as well. For example, long life man made products were used for roofing, siding, trim board, decking, railing and soffit applications. We also took advantage of locally sourced products wherever possible, but never to the detriment of life cycle. For instance, all the ground cover (bark mulch or wood chips) were either created on site with site materials or made 25 minutes away from wood waste products. Also, our large architectural timber frames, timber trusses, and wood beams were fabricated by a millwork shop just ¼ mile away, from domestic, sustainable forest timbers.
HERS Index:
Energy Star Score:
Annual renewable energy generated:
Electric Utility Company:
Datasets and Utility Bills sources and reliability:
Monthly Unitil readings (bills) have been retained since interconnection of the PV system (Dec 2011). Project construction completion (occupancy) occurred in August, 2012. Data taken from the calendar years 2013, 2014, and 2015 have been used for the purposes of this case study.
Electricity amount (imported from grid):
Electricity amount (credited or exported to grid):
Net electricity usage (purchased electricity):
Natural gas amount (purchased energy):
Energy Storage Capacity:
Energy Storage type:
THERMAL
Stage 1-A 198 gal solar water storage tank is used to store domestic water supply from the 9 panel roof collectors. Max temperature settings used vary from 130-160 deg F over the year.
Stage 2- Secondary hot water (glycol) is used (from either lower grade heat from the solar thermal panels or high grade heat from the panels above the max set point of the 198 gal tank) to heat the geothermal system's buffer tank up to a max of 110deg F through a stainless steel heat exchanger.
Stage 3- Secondary hot water (glycol) is used (from either lower grade heat from the solar thermal panels or high grade heat from the panels above the max set point of both the 198 gal tank and geothermal buffer tank) is used to heat the geothermal system's wet sand bed located below the sub-slab insulation layer using (13) 300’ long horizontal ground loops that dispense BTU’s into the 12” deep, saturated sand geothermal bed to boost the energy available in the bed. Measured ground (sand) temperatures vary through the course of the year from approximately 40deg F (winter) to 75deg F (summer) over a 12 month cycle.
9 loops for each system run underneath the 6" eps foam below the lower level concrete floor. 4 loops run underneath 6" eps foam located outside the foundation walls on the south side of the building beneath 8-10 feet of earth fill. During summer cooling mode, the 4 outside loops become dedicated to geothermal cooling via a zone control valve on each system, while the 9 interior loops continue to store excess heat from the solar thermal panels.
ELECTRIC
A bank of 16 DC, 255 amp-hour batteries are also connected to the PV system through two 3,600W DC Outback inverters and can supply up to 7,200W of and 49 kWh of back-up emergency power if the utility grid goes down.
Subslab assembly:
-4" Reinforced concrete w/radiant floor tubing
-6" EPS foam insulation
-Taped and sealed vapor barrier.
-12" sand bed which houses both the glycol filled gound loops from the solar hot water panels (upper layer) and the water filled ground loops (lower layer) from the geothermal heat pumps.
-Natural grade or compacted fill
Slab edge assembly:
The lower level walls are 8” Logix ICF concrete walls with 2-3/4” of high density foam on each face with an R27 insulation value extended down past the edge of slab to the frost line and wall footing. No further slab edge treatment is required.
Foundation wall assembly:
The lower level walls are 8” Logix ICF concrete walls with 2-3/4” of high density foam on each face with an R27 insulation value extended down to the frost line and wall footing.
Above grade wall assembly:
The upper walls are double 2x4 at 24” on center, wood stud walls separated by a 3.5” cavity. The outer wall and cavity have 7” of dense pack cellulose insulation and vapor barrier. The inner wall (inside the vapor barrier) is insulated with 3.5” of rockwool insulation.
Flat attic assembly:
The roof trusses have a minimum of 24” of blown-in cellulose insulation. All flat ceilings areas (cosmetic only) are insulated above as part of the roof truss assembly. Penetrations for down lighting fixtures occur through the cosmetic ceilings, not through a vapor barrier. The roof trusses have a minimum of 24” of blown-in cellulose insulation above the ceiling vapor barrier. All penetrations through the vapor barrier occur at predetermined locations between the trusses that are fitted with a pre-made insulated box to allow for proper sealing of the vapor barrier. Blower door testing was conducted both before and after installing of the interior drywall.
Cathedral ceiling assembly:
The roof trusses have a minimum of 24” of blown-in cellulose insulation. All flat ceilings areas (cosmetic only) are insulated above as part of the roof truss assembly. The roof trusses have a minimum of 24” of blown-in cellulose insulation above the ceiling vapor barrier. All penetrations through the vapor barrier occur at predetermined locations between the trusses that are fitted with a pre-made insulated box to allow for proper sealing of the vapor barrier. Blower door testing was conducted both before and after installing of the interior drywall.
Door Area:
Space heating - Manufacturer & Model:
Space heating - capacity:
Space cooling - Manufacturer & Model:
Space cooling - capacity:
Domestic hot water - Manufacturer & Model:
Domestic hot water - capacity:
Ventilation - Manufacturer & Model:
Process:
Others have used the term “house for life” and we couldn’t agree more with that concept. This house was built with the best, most cost effective list of sustainable/durable materials we could find in 2011-2012 after countless hours (years) of product research and three consecutive years of consultations with manufacturers at the annual International Builders Show (IBS).
The concept for creating the ROSE Cottage Project started many years prior to actually procuring the site, as it took almost 2-1/2 years to close on the purchase of the property. Once the closing took place in September of 2010, we immediately engaged a logger and a site contractor in October to clear trees, rough in a 700' long access drive, and rough prep the building site. Work was shut down in December 2010. The next 6 months were used to complete the final design, select and specify materials, engage contractors, and prepare to commence with construction. During that time period, the owner, architect, engineers, and builders worked closely together to refine and finalize the design of the project. Site work resumed in July, 2011 and the house was occupied in August, 2012 .......roughly a year later. The first structure to be erected was the detached carriage style garage/barn, which allowed us to install the 13.8kw PV installation and go on-line with Unitil on December 10, 2011 ........and from that point forward we were building using our own solar power!
Design for Adaptability:
Our commitment to creating a flexible design that can fit the needs of several types of multi-generational occupants is a perfect match to the investment in a zero net energy home that generates as much energy from renewable sources, as it uses. Not everything needs to be built day one, but the ability to easily add or change a building needs to be well understood in advance. Grab bars, shower seats, and automatic door openers (the list goes on) may never be needed, but they do need to be planned for. Sometimes planning means blocking, sometimes it means pre-wiring, but mostly it requires spatially thinking ahead.
One story aging-in-place living is accomplished on the upper at-grade level. Given the extraordinary expense of assisted care and/or nursing home living, a modest investment in making a new home suitable for people to grow old in adds significant value to the home. A stacked washer-dryer laundry area across from the first floor powder room is sufficient to serve an older couple if/when the larger, lower level laundry room is no longer an option due to physical limitations. The garage has an extended depth and houses a dry cold storage room, as well as a 4′ wide ramp up the three steps to the entry area. The garage width is also enlarged for easier car egress and mobility. Groceries can be “wheeled” in using a simple 2-wheel, lightweight, aluminum cart. The outdoor spa is sunken into the deck with an inclined grab bar to facilitate an older person’s easy entry, and the deck is roofed over to facilitate year round, all-weather use.
All of the passage doors on both levels are 36″ wide (34″ for pocket doors). The large NanaWall folding/sliding door to the 3-season room has an ADA threshold, and there is no step down from the interior space to the 3-season room. Space has been allocated in the home for wheelchair mobility and access. Simple ramps can be easily added later (if required) to transition the 8″ differential height from the home’s interior to the outside elevated rear deck. Pre-wiring and blocking has been included to allow for automatic door operator systems to be installed later (if required) on the entry door from the garage which already incorporates an ADA threshold.
Since we are already focusing on an aging-in-place design, the lower level can be immediately used as a one level, two bedroom, in-law suite or caregiver suite by using all the lower level finished space as a “two family” style, two bedroom apartment. It can also transform into a one bedroom caregiver suite by adding one simple straight partition wall to divide the large “gathering” space area in half; thereby splitting up the lower level space for dual use between upper and lower occupants, each side having one bedroom. The multi-purpose gathering space already has a compact, fully functioning kitchen along one wall, along with a combination of carpeting and porcelain floor tile for mixed use. Laundry, bathroom, and storage space all exist on the same lower level. Direct access and parking for the lower level is also provided at the rear of the home. Alternatively, the same space could be used immediately for a younger extended family. There is ample outdoor living space at each level (deck or patio).
On the energy front, a concrete foundation was built with 4 embedded threaded anchor bolts, next to the detached garage to allow the addition of a wind turbine in the future, if desired. The electrical interconnection would occur immediately at that location as well. There is a dedicated circuit in the attached 2-car garage for EV charging, if desired. Additionally, there is an outside circuit panel located in the rear of the building at the lower grade level, if someone wanted to expand the development of the outdoor living spaces in some manner.
Other Software tools:
Autocad
Revit
Energy Modeling Software:
REM/Rate software for Energy Star Rating
Trane Trace
Outcome of project goals:
The project, known as the ROSE Cottage Project, was the first to be undertaken using the “ROSE Construction Method” plan for developing zero net energy homes. It is featured on the RCMZeroEnergy.com website www.RCMZeroEnergy.com and Facebook page www.Facebook.com/RCMZeroEnergy to share the knowledge and explain reasons behind the approach. The purpose of both are to educate owners, designers, builders, and developers to the how’s and why’s of undertaking high performance residential construction that starts with high performance enclosure design and ends with renewable energy technologies. If anything is certain, it is the uncertainty of the energy markets over the past 40+ years, and that is likely to continue. Assumptions inevitably prove to be wrong on energy pricing. There has to be reasons to design and build high performance projects like this other than the pure economics of energy pricing, because you have to assume too much. The recent advances in natural gas and crude oil fracking in the United States may change the energy landscape once again, as it relates the commodity pricing of fuel and electricity. We could be on the cusp of a prolonged period of relatively “cheap” energy again for some markets, or maybe not. So, unless you are automatically stuck with using propane, oil or grid electricity, we all have to discover the inherit benefits of sustainable, energy efficient living that go past the simple return on investment (ROI), because the economic benefits alone can change as fast as the stock market.
The owner developed this project to demonstrate that there are in fact many aspects of a zero net energy or near zero net energy project approach that have far reaching benefits beyond ROI. Our experience shows that without ever reaching into our renewable power bag of tricks, or double wall construction, to get to net zero; below 60 on the HERS index is readily achievable on just about any site with just about any style home with the right approach to enclosure design regarding air tightness, thermal performance, and efficient use of energy. Sixty (60) is really the starting point that any homeowner should ask for and any builder should strive for; however, getting there will take a great deal of education to the how’s and why’s of enclosure construction. Most renewable energy options that we currently have at our disposal can be planned for later inclusion into a project and can be economically added to a project at a later date based upon the cost of energy, or the owner’s ability to fund the extra costs of eliminating their fuel supply. Saying it another way, do it for the ROI when energy prices rise, or do it when you can afford it, or both. For these reasons, and many more that we hope to continue to demonstrate on the website: do it now if you can afford to, and hopefully do it later if you can’t.
We don’t have all the answers and there is no ONE way to accomplish the end goals. But the more high performance projects that are designed and built; the greater the knowledge base; the easier it will be; and the lower it will cost for everyone. The market will change. Construction practices will change. Owners will purchase a better product if it is available. We will be more efficient and we will use fewer resources.
Discrepancies:
Actual performance has exceeded predicted performance to date, requiring no changes to the project. The project has banked electrical energy (below zero net) for each of the first three full years of operation (2013, 2014, 2015), and we see nothing midway through 2016 to change that course.
Finances Description:
This project, unlike most, was not approached with a fixed budget. Given the initial cost of the unique size (almost 9 acres) and location (City of Concord, but adjacent to a pond) of the raw land, as well as the anticipated costs of developing the site, we knew the added costs of going "zero net" would not drive the final costs as much as would be the case if this was a simple city or suburban type lot. Extra costs were also allocated for considerable outdoor living spaces as well as a second (detached) garage/barn outbuilding. Additionally, some of the non-energy related residential features/costs were specifically done to demonstrate that a ZNE home need not be small, boxlike or unattractive ......as some of the earlier (pre-2010) examples had been. Further, the secondary goals of an aging-in-place design with a multi-generational use capability also added to some of the project costs. Having said all that, our goal was still aimed at keeping the actual residential building costs (including all net costs of the renewable energy systems) to below $200/sf of conditioned space, which we did at $175/sf.
Total Cost of Project:
Construction hard cost:
Gross Cost of Renewable Energy System:
Value of Tax Credits for renewable energy systems:
Net Cost of renewable energy systems:
Federal incentives:
30% Investment Tax Credit on all qualifying energy technologies
State incentives:
Solar Hot Water Incentive- $1,900
Utility incentives:
Certified Energy Star Home Builder's Incentive - $4,500
Annual Electric Savings:
Annual Revenue from SRECs or other renewable energy credits:
Advice:
Take advantage of whatever rebates or incentives are available at the the time of project development, as they may vary at any specific period of time of project development. Rebates and incentives are not the "drivers" of creating a ZNE project, they simply lower the entry cost. Use the cost of the electricity producing component (ex- PV panels) as the means to drive the HERS # from less than 30-35 (near net zero) ...... to 0 "net". Future utility rates may offer less than full retail off-set value for net metered power that flows into the grid when real time production exceeds use, which will lower some of the monetary value created through self generation and the financial benefits of achieving zero net status.
The total return on investment goes far beyond the annual electrical savings estimated at $3000/yr on a current cost basis, as there are no fuel costs associated with the annual operation of the home beyond the tiny amount of propane used for the stove cook top. The outdoor spa, which uses about 1500 kWh/year, is included in these numbers. The spa uses approximately 10% of the output of the PV panels on an annual basis. With a minimum life expectancy of 25 years for the electrical/mechanical technology installed, combined with the inflation related costs of fuels and grid provided electricity, an attractive ROI could still be represented if that was your only driving force for going zero net.
The installed cost of PV systems today (2016) are far more competitive as panel costs continue to decline and the number of installers increase. However, we feel we received a very competitive price (exclusive of battery store) for the time (2011) these were installed. The simple payback for this system is approximately 10 years. SRECs have not yet been sold for this project.
Additionally, as this was our first Geo-Solar Hybrid residential installation, we believe the cost of the same sized system now (2016) would be reduced by at least 1/3 through further simplification for residential applications as well as increased mechanical contractor competition and equipment pricing. The simple payback for the increased cost above a conventional propane fired heating and cooling HVAC system for this project is approximately 15 years, which would fall to about 10 years if costs were reduced by 1/3.
Published References:
http://rcmzeroenergy.com/ROSE-Cottage-Project/project-overview.html CASE STUDY - RCMZEROENERGY.com WEBSITE 2014
http://www.nhhomemagazine.com/March-April-2015/Building-a-net-zero-home-... NEW HAMPSHIRE HOME MAGAZINE APRIL-MAY 2015
http://www.treehugger.com/green-architecture/you-will-want-live-rose-cot... TREEHUGGER JAN 2013
http://mechanical-hub.com/bosch-announces-2013-green-living-award-winners BOSCH GREEN LIVING AWARD 2013
http://www.bosch-climate.us/files/201308202022140.ROSECottage-CaseStudy-... BOSCH CASE STUDY 2013
https://hastingsview.com/2014/01/13/peoples-choice-winner-netzero-and-a-... 2013 MARVIN ARCHITECT'S CHALLENGE SHOWDOWN PEOPLES CHOICE WINNER
https://www.youtube.com/watch?v=O5b5fVvO_CE&feature=youtu.be 2013 MARVIN ARCHITECT'S CHALLENGE SHOWDOWN PEOPLES CHOICE WINNER
http://www.jetsongreen.com/2014/02/rose-cottage-proves-a-large-home-can-... JETSON GREEN 2014
http://www.mnn.com/your-home/remodeling-design/blogs/rose-cottage-a-net-... MOTHER NATURE NETWORK 2014
http://www.nanawall.com/blog/adjustable-home NANAWALL BLOG 2013
https://www.youtube.com/watch?v=jEh404Dq9O4 NANAWALL YOUTUBE 2013
http://www.cnet.com/news/bosch-pushes-sensor-tech-green-building-and-aut... FEATURED BY BOSCH @ CES 2014
http://gbdmagazine.com/2014/27-hl-turner/ GREEN BUILDING & DESIGN 2014
http://www.proudgreenhome.com/news/zero-energy-building-construction-mov... PROUND GREEN HOME OCT, 2014
http://www.prnewswire.com/news-releases/turner-group-wins-three-cornerst... CORNERSTONE AWARDS (3)
http://greenbuildingelements.com/2014/09/30/net-zero-buildings-future-co... GREEN BUILDING ELEMENTS SEPT, 2014
http://www.prnewswire.com/news-releases/the-h-l-turner-group-inc-awarded... USPTO AWARDED 2014
http://us3.campaign-archive1.com/?u=439839742a4f304f229273a83&id=e30f67c32a THE ZERO NET E-NEWSLETTER 2014
https://www5.eere.energy.gov/buildings/residential/partner_profile/1003 Turner Building Science & Design DOE Zero Energy Ready Home: Partner Profile
http://www.wmur.com/money/some-nh-residents-selling-excess-electricity-b... Harold Turner - WMUR TV Appearance on Net Metering
http://www.prnewswire.com/news-releases/the-h-l-turner-groups-award-winn... RCMZEROENERGY.com NEWSLETTER APRIL, 2014
http://www.proudgreenhome.com/whitepapers/rose-cottage-relies-on-bosch-f... PROUD GREEN HOME NOV, 2013
http://www.houzz.com/projects/334244/The-ROSE-Cottage-Project HOUZZ
Special architectural measures:
The project is comprised of two separate structures connected by a 70-foot diameter courtyard. The house and attached two car garage follow the natural sloping terrain, facing south-east with views towards the pond, woodlands and wetlands. Three distinctive staggered, rectangular volumes make up the garage, main living space, and master bedroom wing (with 9 thermal solar panels on the roof); accented by a timber framed, gable main entrance that offers transparency and a visual link to the pond beyond. Off the rear of the main living area at the upper level are two timber trussed, gable roof spaces each extending 16' out from the rear wall of the home, which are elevated and connected by an open wood framed deck. The first space is an enclosed 14' x16' three season room which shares a common 12' folding/sliding glass door assembly with the dining area. The second space, housing a sunken spa, is a 14' x 20' roofed deck area that is accessed off the foyer/main entry and is contiguous with the open deck connecting to the three season room. The lower level of the home is below grade on three sides, with two rear at-grade entrances, and is washed with natural light from oversized windows and sliding glass doors facing the pond. Radiant floor heating is incorporated at both levels and is powered by a 2T geothermal heat pump. The detached carriage style garage faces north and its long sloping roof to the south supports 60-230W photovoltaic solar panels, yet it nestles itself comfortably into the sloping terrain on two sides with raised concrete foundation walls.
The envelope of the house is super-insulated with R40 value upper walls, R27 value lower walls, and R60 value roofs. The upper walls are double 2x4 at 24” on center, wood stud walls separated by a 3.5” cavity. The outer wall and cavity have 7” of dense pack cellulose insulation and the inner wall is insulated with 3.5” of rockwool insulation. The lower walls are 8” Logix ICF concrete walls with 2-3/4” of high density foam on each face. The roof trusses have a minimum of 24” of blown-in cellulose insulation. Under the lower level 4” slab-on-grade is 6” of EPS foam insulation which is R22+. The roofs are all pitched using prefabricated roof trusses that allow for a minimum of 24" of blown in cellulose. The top chords are extended using supplemental on-site lumber to create a standardized 24" overhanging soffit for summer shading and continuous air flow to the ridge vents. Likewise, the gable ends receive similar treatment to provide a 24" shading overhang.
Heating and cooling are provided by two Bosch 2 ton ground-source heat pumps connected to a horizontal ground loop system. One heat pump is a Bosch water-water model and the other a Bosch water-air model. The water-water unit is solely devoted to heating the ten zone radiant floor system on two floor levels, a Runtal hydronic towel warmer/radiator in the master bath, and the 198 gal Bosch/Buderus PL750/2S Solar DHW/Space Heating Combi Tank. The solar tank is kept at a minimum of 100 deg F by the heat pump during periods of poor weather. The water-air heat pump serves a single upper level ducted distribution system that has operable adjustment dampers in the ductwork to allow the owner to create both warm and cool spaces. The upper level air system is controlled by a centrally located “smart” Ecobee thermostat and a mechanical room Ecobee control panel, which is also accessible on-line via a PC or smart phone app, to provide both heating and cooling control at all times. Nine of the ten radiant zones are controlled by simple heat only wall thermostats, and the largest open space 1st floor zone is controlled by the Ecobee thermostat which decides how best to heat that zone (i.e. - capable of running both heat pumps simultaneously).
Domestic hot water is generated by a 9 panel (28,000 btu/day/panel capacity) Bosch/Buderus Logasol SKS 4.0 flat plate collector solar system that stores energy in the 198 gallon Bosch Combi storage tank in the lower level mechanical room. Whenever the solar hot water is below 120 deg F, a Seisco on demand electric water heater boosts the water coming from the hot water tank to approximately 135 deg F before reaching a final tempering valve. The solar panel system panels are also utilized to form a solar-geothermal “hybrid” system, such that once the solar storage tank reaches peak temperature (160 deg F in summer), the hot glycol coming from the panels is diverted through a stainless steel heat exchanger via a Bosch/Buderus TR0603 Solar Controller to heat a small buffer storage tank up to 120 deg F. The buffer storage tank is also heated by the 2 ton water-water geothermal heat pump and serves the radiant floor heat system on both levels. The buffer tank temperature is automatically maintained by the heat pump to between approximately 90-110 deg F, based upon the outdoor temperature. When the buffer tank is in active heating mode during the winter season, the BTU’s from the solar glycol go directly into the space heating needs of the radiant floors when not heating the solar tank’s domestic hot water supply. If the buffer tank reaches its maximum heat setting of 120 deg F, the hot glycol feed is then diverted into (13) 300’ long horizontal ground loops that dispense BTU’s into the 12” deep, saturated sand geothermal bed to boost the energy available in the bed. The (13) 300’ long geothermal ground loops are separated vertically from the glycol loops by 4” of wet sand. When the glycol temperatures (usually lower than 115 deg F) are too low to either heat up the buffer tank or solar tank, flow is automatically diverted into the sand bed (“solar dump”).
Energy Strategies:
Heating and cooling are provided by two Bosch 2 ton ground-source heat pumps connected to a horizontal ground loop system. One heat pump is a Bosch water-water model and the other a Bosch water-air model. The water-water unit is solely devoted to heating the ten zone radiant floor system on two floor levels, a Runtal hydronic towel warmer/radiator in the master bath, and the 198 gal Bosch/Buderus PL750/2S Solar DHW/Space Heating Combi Tank. The solar tank is kept at a minimum of 100 deg F by the heat pump during periods of poor weather. The water-air heat pump serves a single upper level ducted distribution system that has operable adjustment dampers in the ductwork to allow the owner to create both warm and cool spaces. The upper level air system is controlled by a centrally located “smart” Ecobee thermostat and a mechanical room Ecobee control panel, which is also accessible on-line via a PC or smart phone app, to provide both heating and cooling control at all times. Nine of the ten radiant zones are controlled by simple heat only wall thermostats, and the largest open space 1st floor zone is controlled by the Ecobee thermostat which decides how best to heat that zone (i.e. - capable of running both heat pumps simultaneously).
Energy Use and Production Documentation:
Subslab R-value:
Slab edge R-value:
Foundation wall R-value:
Above grade wall R-value:
Flat attic R-value:
Cathedral ceiling R-value:
Average window U-factor:
Solar Heat Gain Coefficient:
Visible Light Transmittance:
Door U-Factor:
Cost per square foot of Conditioned Space:
Air Changes per hour, ACH50:
Project Photos:


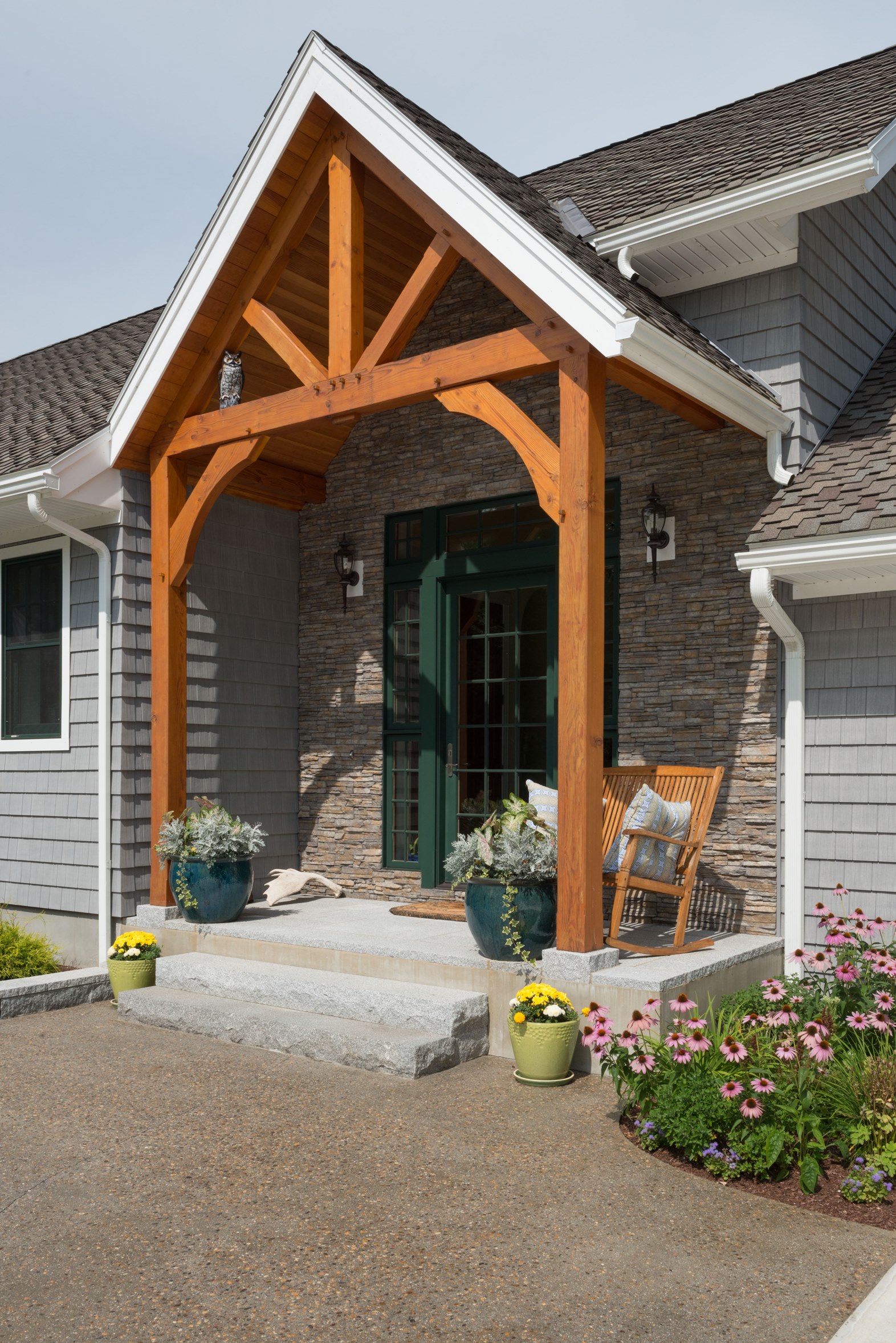
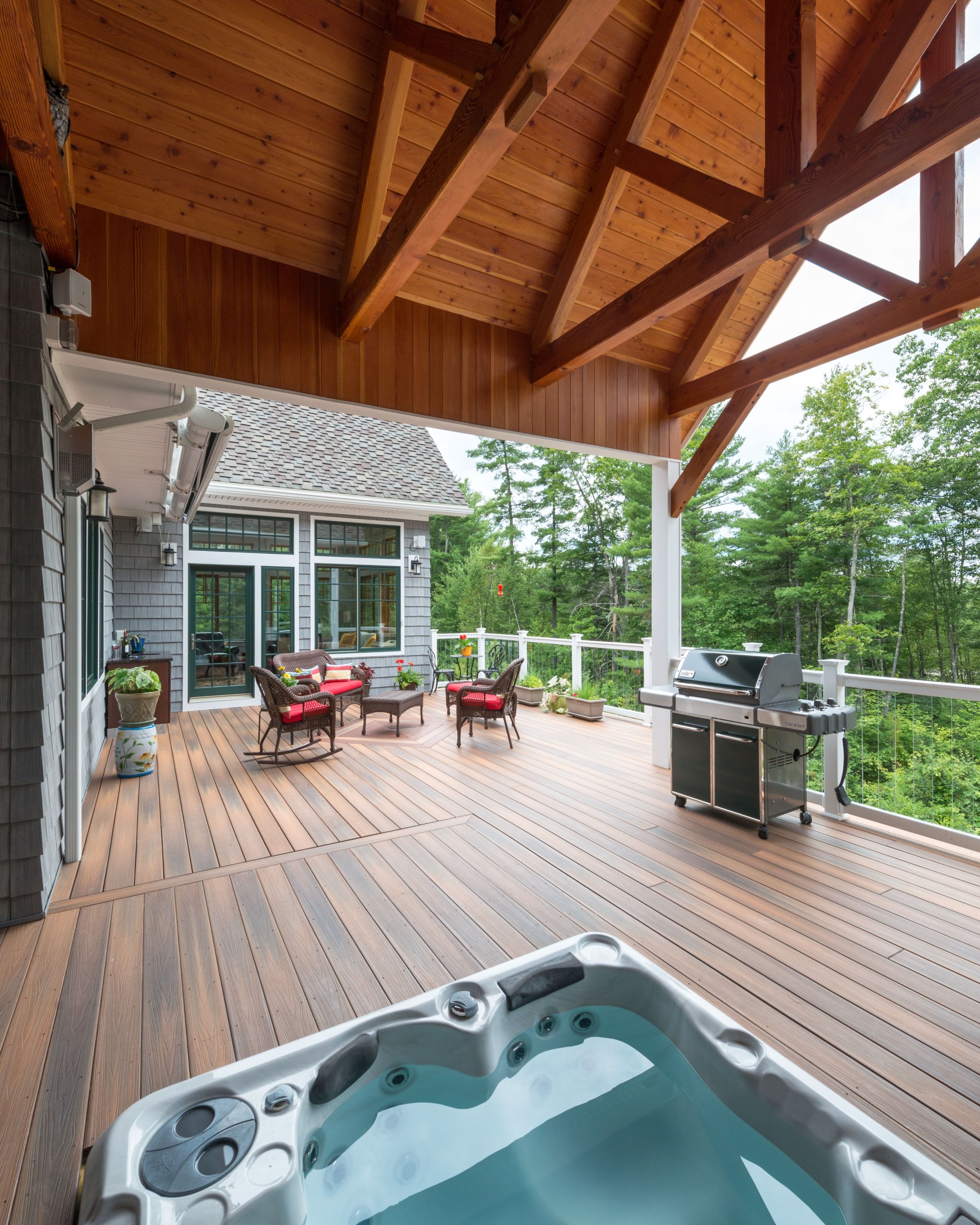
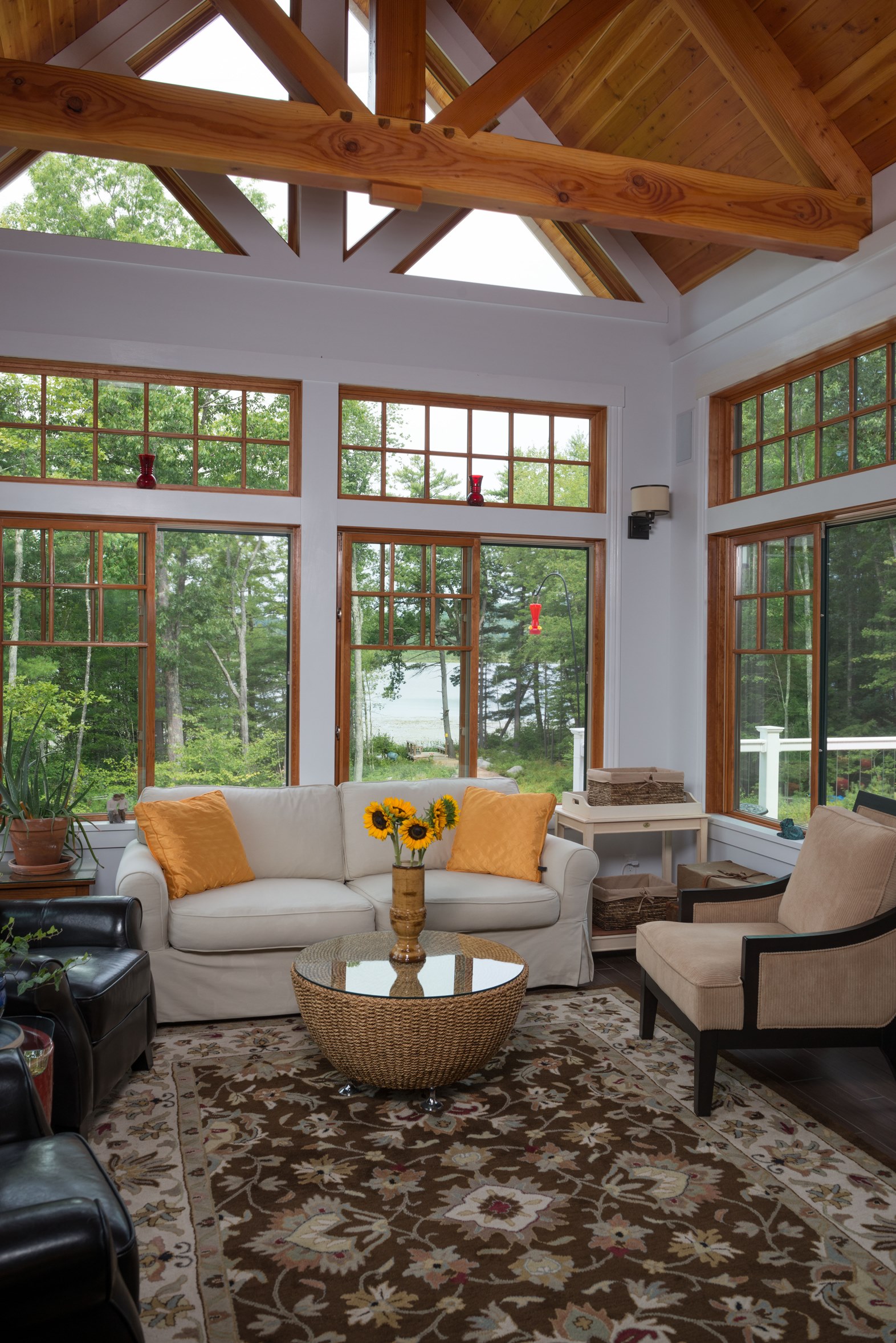
Number of Bathrooms:
Scope Description:
Located in a rural neighborhood section of the capital city of Concord, New Hampshire, this multi-generational, aging-in-place house demonstrates how a zero net energy, sustainable residence can be built within a reasonable budget to incorporate multiple themes of long life cycle value. One of the first zero net homes in northern New England, the house occupies a 2.12 buildable footprint surrounded by 6.74 acres of conservation easement land along the shore of Turtle Pond. The project is comprised of two separate structures connected by a 70-foot diameter courtyard. The house and attached two car garage follow the natural sloping terrain facing south-east with views towards the pond, woodlands and wetlands. Three distinctive rectangular volumes make up the garage, main living space, and bedroom wing; accented by a timber framed, gable main entrance that offers transparency and a visual link to the pond beyond. Off the rear of the main living area are two timber trussed, gable roof spaces each extending 16’ out from the rear of the home, which are elevated and connected by an open wood framed deck. The first enclosed space is a 14’x16’ 3-season room which shares a common 12’ NanaWall folding/sliding glass door assembly with the dining area. The second partially enclosed space opens off the foyer/main entry onto an open deck and sunken spa that is contiguous with the open connecting deck. The lower level of the home is below grade on three sides, with two at-grade entrances from the rear, and is washed with natural light from oversized windows and sliding glass doors facing the pond. The detached carriage style garage faces north and its long sloping roof to the south supports 60 photovoltaic solar panels, yet nestles itself comfortably into the sloping terrain on two sides.
Site conditions:
Renewable Energy Sources:
Other Purchased Fuels Description:
Less than 50 gal of propane per year is purchased to supply a gas stove cook top and an architectural gas fireplace.
Storage Strategies & System Details:
A bank of 16 DC, 255 amp-hour batteries are also connected to the PV system through two 3,600W DC Outback inverters and can supply up to 7,200W and 49kWh of back-up emergency power if the utility grid goes down.
Summary of enclosure strategy/description:
The envelope of the house is insulated with R40 value upper walls, R27 value lower walls, and R60 value roofs. The upper walls are double 2x4 at 24” on center, wood stud walls separated by a 3.5” cavity. The outer wall and cavity have 7” of dense pack cellulose insulation and the inner wall is insulated with 3.5” of rockwool insulation. The lower walls are 8” Logix ICF concrete walls with 2-3/4” of high density foam on each face and extend fully up to the first floor level 3/4" engineered floor decking. First floor framing is located between and attached to the ICF walls, not on top of the ICF walls. The roof trusses have a minimum of 24” of blown-in cellulose insulation. Under the lower level 4” slab-on-grade is 6” of EPS foam insulation which is R22+.
Radiant floor tubing on the upper floor is an Uponor staple up system with an insulation barrier, while the lower floor is a 4" thick concrete floor with embedded Uponor tubing.
The roofs are all pitched using prefabricated roof trusses that allow for a minimum of 24" of blown in cellulose. The top chords are extended using supplemental on-site lumber to create a standardized 24" overhanging soffit for summer shading and continuous air flow to the ridge vents. Likewise, the gable ends receive similar treatment to provide a 24" overhang.
Given the use of double wood stud wall (R40+) exterior wall construction on the upper level and Logix ICF (R27) concrete on the lower level walls, any type of exterior door was a significant drop-off in thermal performance, so it only made sense to use the french style doors (5 total) as daylighting features as well, which allowed a reduction in the total windows required for great natural light. Including features like the operable sidelites to the two main entry doors added to the natural ventilation options. Additionally, placing a large (8’x8’) french slider door on the lower level directly below the (12’x8’) NanaWall folding/sliding glass door assembly above on the upper level leading into the 3-season room, permits the lower level to be completely protected from summer rains, allowing it to be open even during inclement weather, just like the entry sidelites. The large slider also floods enormous amounts of light into the lower level.
Roof Assembly:
All roofs are pitched using deep roof trusses. The roof trusses have a minimum of 24” of blown-in cellulose insulation.
Roof R-value:
Window Description:
1) Wood Frame w/Alum Cladding, Marvin, Ultimate Tri-Pane, DBL Hung, Low E Argon (0.25 U, 0.23 SHGC, 0.36 VLT) Upper Level
2) Wood Frame w/Alum Cladding, Marvin, Ultimate Tri-Pane, Fixed, Low E Argon (0.25 U, 0.23 SHGC, 0.36 VLT) Upper Level
3) Fiberglass, Marvin Integrity Ultrex, DBL Hung, Low E Argon Lower Level
4) Fiberglass, Marvin Integrity Ultrex, Fixed, Low E Argon Lower Level
5) Fiberglass, Marvin Integrity Ultrex, Glider, Low E Argon Lower Level
6) Fiberglass, Marvin Integrity Ultrex, Awning, Low E Argon
6) Fiberglass, Marvin Integrity Ultrex, Casement, Low E Argon
Door Description:
1) Wood Frame w/Alum Cladding, Marvin Ultimate, Inswing French Door, Low E Argon
2) Fiberglass, Marvin Integrity Ultrex, Inswing French Door, Low E Argon
3) Fiberglass, Marvin Integrity Ultrex, Sliding Patio Door, Low E Argon
4) Wood Frame, Nanawall Sliding/Folding Door System, Triple Pane, Low E Argon
Number of Bedrooms:
Team Members:
William A. Turner, PE- Building Envelope Engineer, CEO of Turner Building Science & Design, LLC
Harold Turner, PE- Developer/Owner, CEO of The HL Turner Group Inc
Steven M. Caulfield, PE,CIH- Mechanical Engineer, President of Turner Building Science & Design, LLC
Paul M. Betch, PE- Structural Engineer, VP of The HL Turner Group Inc
Jeffrey J. Harrison, PE- Energy Consultant, formerly with Turner Building Science & Design, LLC
David Hart, AIA - Project Architect, formerly with The HL Turner Group Inc
Mechanical Equipment Installation Details and Comments:
An experienced commercial grade mechanical contractor was hired for the mechanical install. Rigorous inspections were conducted and installation was guided/coordinated with the manufacturer's (Bosch/Buderus) assistance . Blower door tests were undertaken both before and after drywall installations. Flow hoods used to balance and adjust.
A dedicated make-up air system (exterior hood, duct, gravity damper and floor level diffuser) was designed and installed in the mechanical room for negative pressure associated with the use of the range hood. The range hood is served by an in-line Fantech fan located in the mechanical room that discharges directly to the exterior (not to the ERV). Intake hoods (2) are located on the west wall. Discharge hoods (2) are located on the north wall.
Two floor inspection/measuring ports are installed in the 4" concrete floor in the mechanical room using 4"dia PVC tubes with screw caps. Sensors are located within the tubes to measure ground (sand bed) temperatures at the geothermal tubing level and the solar thermal glycol tubing levels in the ground.
Hand control dampers are installed in the air supply ducts for the master bedroom wing to allow reduction of heat to create cooler room temperatures in the winter months, if desired.
Heating and cooling are provided by two Bosch 2 ton ground-source heat pumps connected to a horizontal ground loop system. One heat pump is a Bosch water-water model and the other a Bosch water-air model. The water-water unit is solely devoted to heating the ten zone radiant floor system on two floor levels, a Runtal hydronic towel warmer/radiator in the master bath, and the 198 gal Bosch/Buderus PL750/2S Solar DHW/Space Heating Combi Tank (i.e.-12 zones total). The solar tank is kept at a minimum of 100 deg F by the heat pump during periods of poor weather when the on-demand Seisco electric heating then boosts the water temp to 130 deg F for domestic distribution.
The water-air heat pump serves a single upper level ducted distribution system located within the lighting soffits. The upper level air system is controlled by a centrally located “smart” Ecobee thermostat and a mechanical room Ecobee control panel, which is also accessible on-line via a PC or smart phone app, to provide both heating and cooling control at all times. Nine of the ten radiant zones are controlled by simple heat only wall thermostats, and the largest open space 1st floor zone is controlled by the Ecobee thermostat which decides how best to heat that large living area (i.e. - capable of running both heat pumps simultaneously), to supply both hot air and a radiant warm floor if required during severe cold conditions.
A simple PVC under slab ventilation loop with 4" dia vertical exit stack was installed for potential Radon mitigation, but later testing proved to not require radon mitigation. The stack dead head is accessible behind a drywall access panel for any possible future need.
On both the east (laundry room and 2nd bath) and south (kitchenette) walls of the lower level, the interior finished walls were bumped out from the ICF using 2x4 studs to create a 12' wide continuous access chase to run wiring and plumbing with permanent access and cleanouts.
In addition to the HVAC systems (heat pumps) and the fresh air system (HRV), there are three isolated in-line Fantech fans that can be manually controlled by adjustable fan speed wall mounted dials at the first floor level. They each consist of an intake louvre near the ceiling of the vaulted space on the upper level, ductwork, in-line fan w/access hatch, and discharge box located near floor at the lower level. Each can be used to move warm air (den, livingroom, and master bedroom) from upper level spaces to add heat to the lower level at times of the year (swing seasons) when daytime temps may be higher than desired at the upper level, but outside night time temps might otherwise call for heat (i.e- storing the heat internally to the building).