Project Subtitle:
Project Description:
The Taft Residence serves as a home and teaching device, supplying one teacher, and his/her family, with a living residence while offering a learning example for the Taft students of how a high-performance home is designed. This private school was founded in 1890 and had an existing residence demolished to build a high performance home that is the Taft School Residence. This home was designed by Trillium Architects to meet Passive House Institute US Certification requirements, as well as ENERGY STAR v3.1, DOE Zero Energy Ready Home, LEED BD+C Homes v4, WaterSense and EPA Indoor airPLUS program standards. This residence includes a 1,400 square foot conditioned basement area below 2,400 square feet of finished space. There is city water, sewage, and natural gas available nearby underground.
Building Type Summary:
Other Awards:
CT Zero Energy Challenge (3rd place), U.S. DOE 2015 Housing Innovation Awards Grand Winner, Residential Award of Honor (CTGBC)
Address:
Lat. / Long.:
Conditioned Floor Area:
Multiple buildings?:
Historic?:
Completion date:
Site description:
An existing residence was demolished to build this new residence.
Materials:
A PV array was installed on the roof to bring site energy consumption to net zero. Used low-VOC sealants, caulks, adhesives, primers and paints. Also used existing granite stones from original house foundation for the steps and stone walls.
HERS Index:
Annual renewable energy generated:
Subslab assembly:
R-28 under slab
Slab edge assembly:
R-20 at slab edge
Foundation wall assembly:
Inside the solid concrete foundation is 3” closed cell foam behind 2x4 stud walls and cellulose in the cavity.
Above grade wall assembly:
Double stud walls have 2¼” closed cell foam plus 8½” dense pack cellulose for a R-49 cavity. The exterior sheathing is R-6.6 Zip Wall System with taped seams to create the continuous air barrier.
Flat attic assembly:
The attic floor is framed with I joists and serves as the top of the building's air-tight envelope, for it has 24" to 36" of blown denspak cellulose insulation both on top and below the floor. The center of the attic floor is double framed with perpendicular boards, so that the HVAC equipment can be between the ceiling and distribution systems and remain in the envelope.
Space heating - Manufacturer & Model:
Space cooling - Manufacturer & Model:
Domestic hot water - Manufacturer & Model:
Ventilation - Manufacturer & Model:
Utility incentives:
Earned $9,000 through the CT Residential New Construction Program
Published References:
Special architectural measures:
Located on a quiet street adjacent to campus the existing, historic home was deconstructed for its efficient replica. Challenged to find high efficiency windows that were historic commission acceptable, the team installed Klearwall awnings or casements over fixed glass (to mimic double hungs) with simulated divided lites (u-values as low as 0.13). A high solar heat gain coefficient (0.58) facilitates the passive solar gain for winter months, while well designed overhangs and pergola shade summer sun.
Energy Use and Production Documentation:
Subslab R-value:
Slab edge R-value:
Foundation wall R-value:
Above grade wall R-value:
Flat attic R-value:
Average window U-factor:
Door U-Factor:
Project Photos:
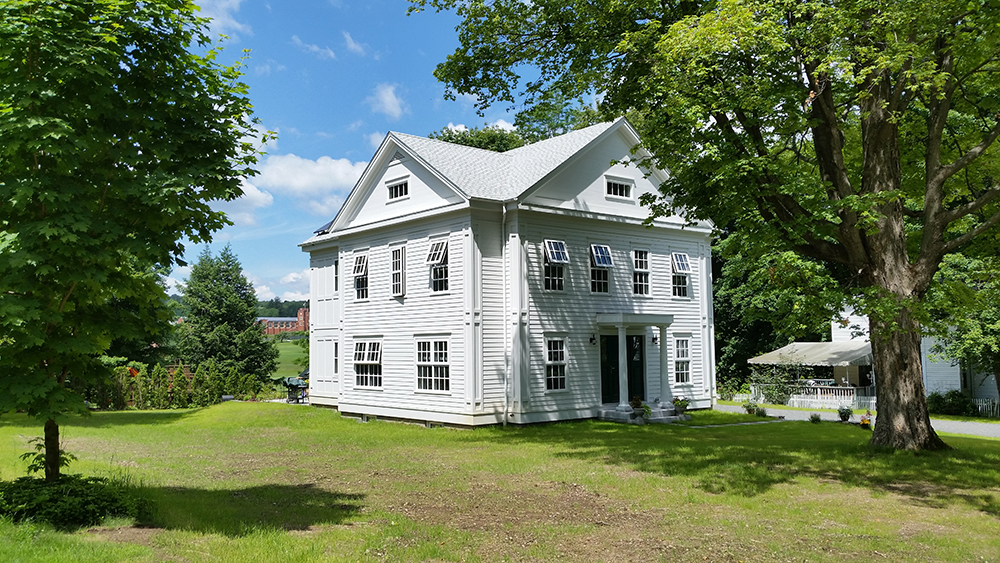
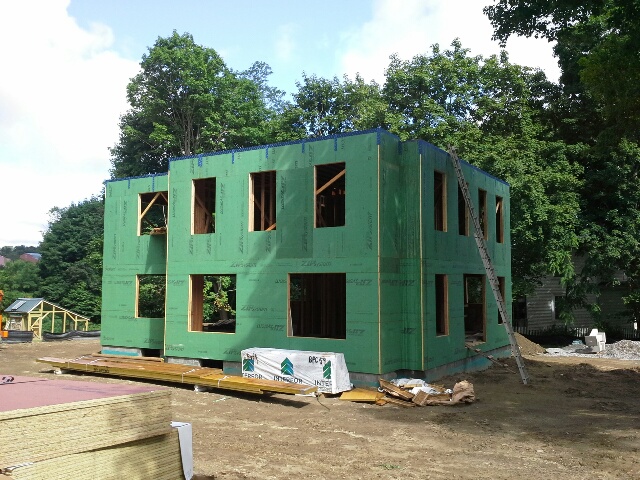
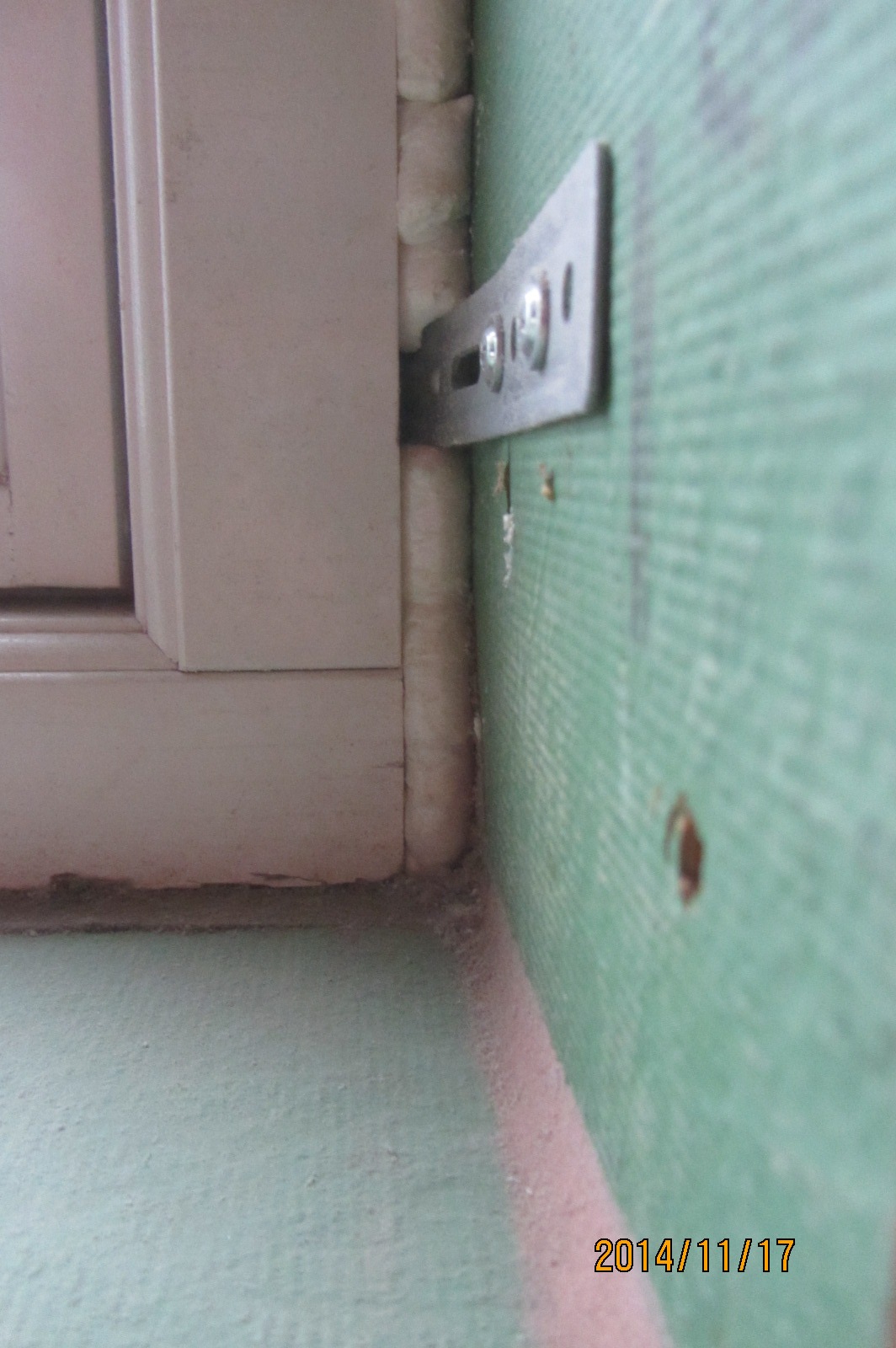
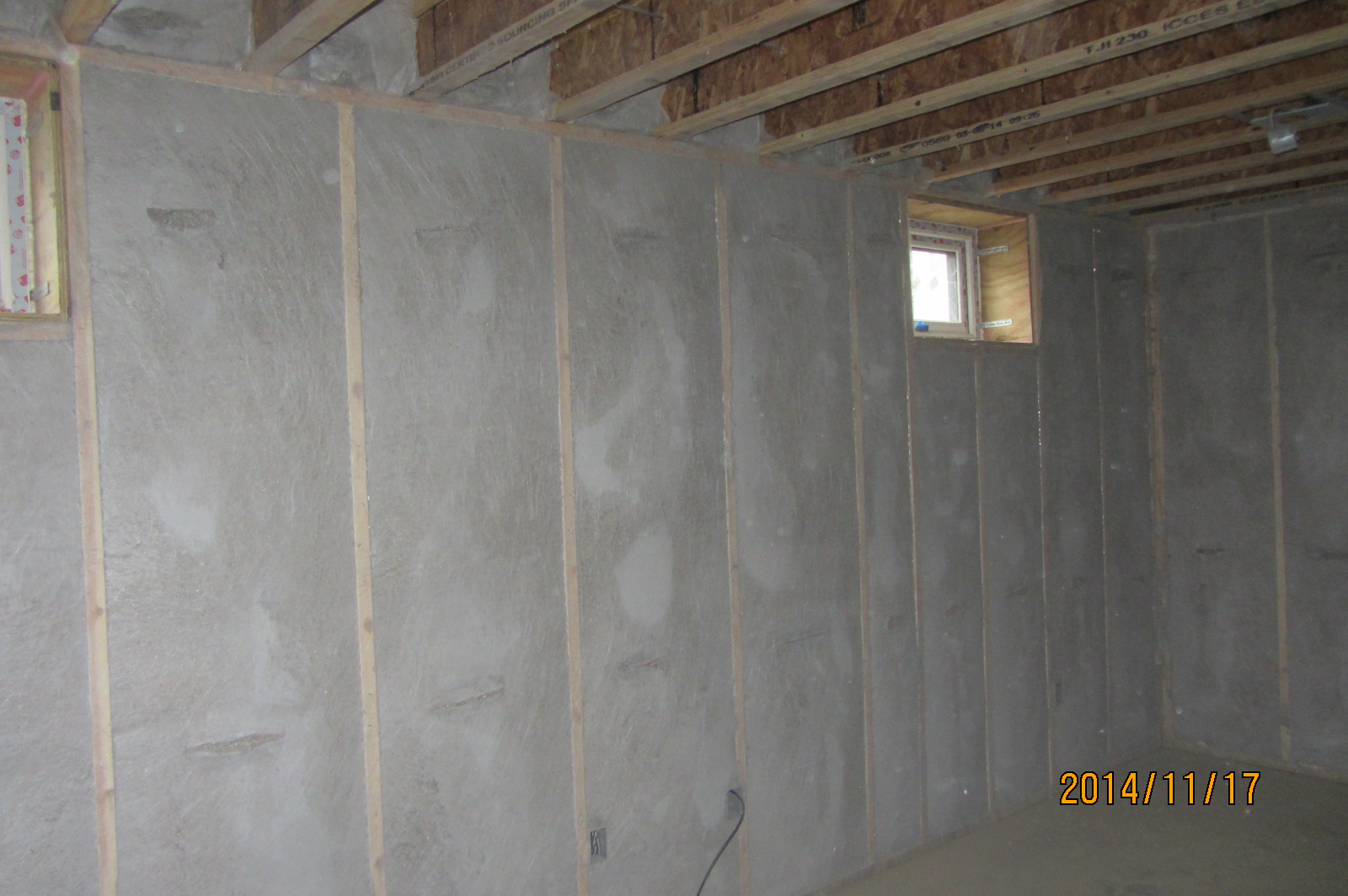
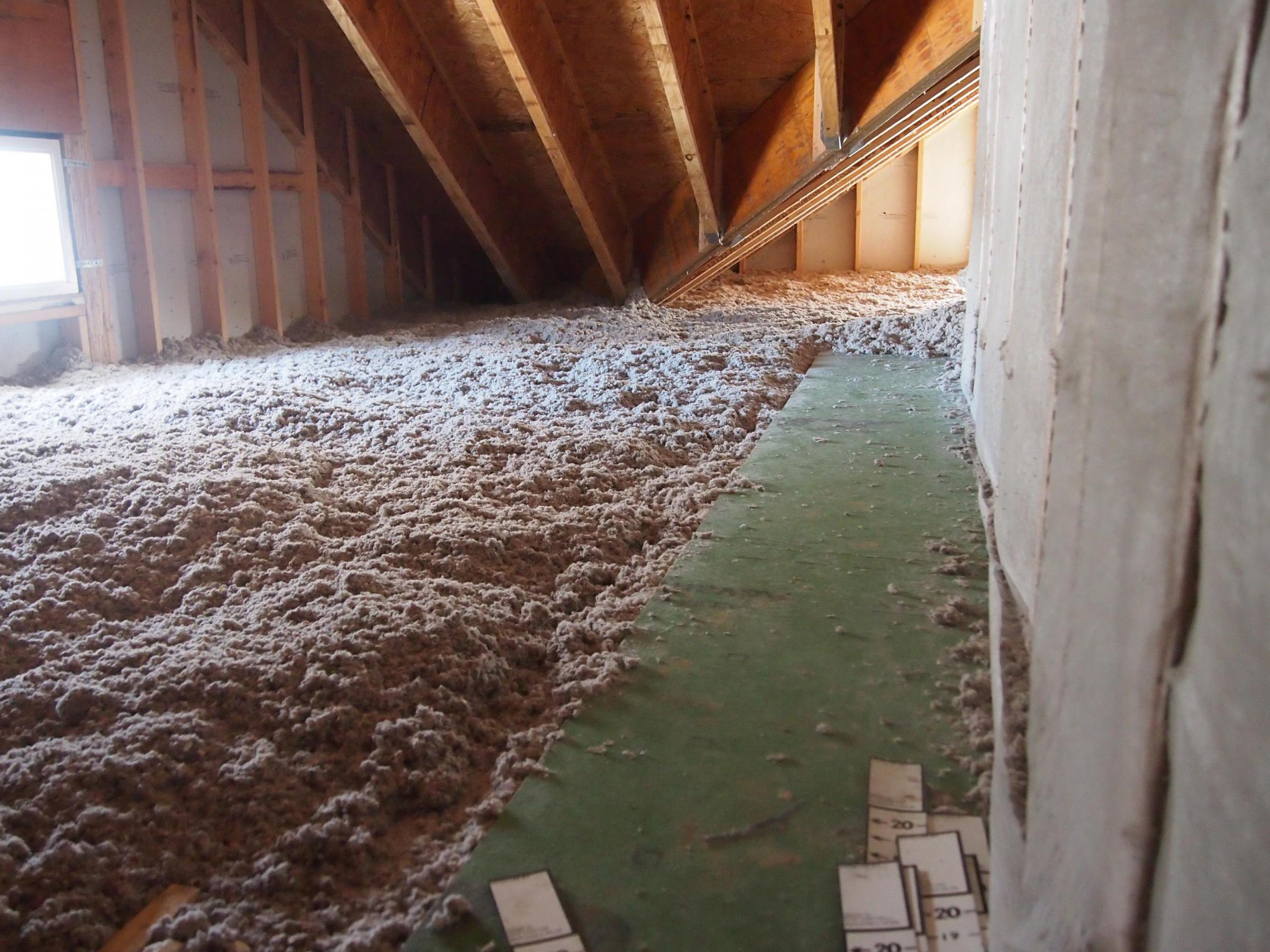
Site conditions:
Renewable Energy Sources:
Summary of enclosure strategy/description:
The Taft School Residence has a durable, very insulated thermal envelope to create an air-tight, bridge-free space.
Window Description:
The windows are made of European Eco-clad & uPVC frames are triple glazed with argon filling and two low-E coatings that have a U-value of 0.11. All rough areas around windows are taped to prevent air leakage.
Door Description:
Similar to the windows, all exterior doors are made of European Eco-clad & uPVC frames are triple glazed with argon filling and two low-E coatings that have a U-value of 0.11. All rough areas around windows are taped to prevent air leakage.
Mechanical Equipment Installation Details and Comments:
Partially ducted air-source heat pumps provide efficient heating and cooling while a heat-pump water heater with occupancy sensors in the baths delivers immediate hot water.